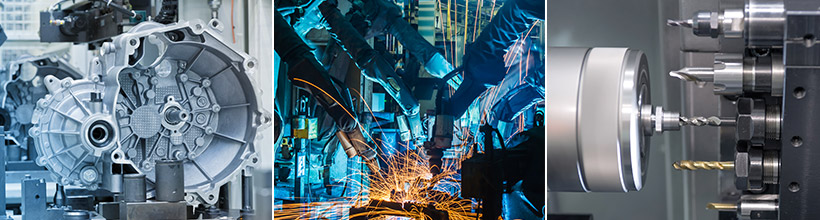 |
|
Machine building
|
As a long-standing partner in machine building and machine design, Micro-Epsilon offers a wide range of sensors and measuring systems. Miniaturized and integrated into machines, displacement sensors measure machine movements, positioning and travel paths and ensure safe machine operation. For automated machines and process-integrated machines, Micro-Epsilon sensors monitor a wide range of sizes of manufactured products. Particularly where harsh ambient conditions such as oil, dirt, pressure, vibrations and temperatures are present, sensors from Micro-Epsilon convince with high precision and favorable conditions. |
|
Condition monitoring of bearings
|
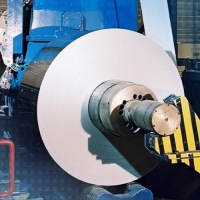 |
Unscheduled downtime of bearings may induce high costs. Early recognition of bearing damage allows for maintenance labor to be performed during scheduled standstills while minimizing costs. Acceleration sensors from Micro-Epsilon are used for early recognition of bearing damage due to their good signal-to-noise ratio. Measuring both static and dynamic accelerations, they are therefore ideally suited to oscillation measurement of bearings with a very low roller speed (≤ 0.2 Hz). Due to high resolution and temperature stability, the sensors are used in measurement tasks for the oil and gas industry, petrochemicals, power generation plants, mining, steel and cement industries and paper manufacturing.
|
|
|
Optimizing weld seams with profile measurements
|
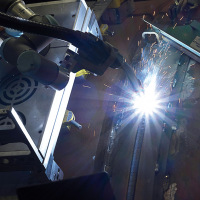 |
Inrotech A/S in Denmark relies on sensors from Micro-Epsilon to achieve optimal quality of weld seams in a fully automatic process. The company has developed a welding robot called »Inrotech-Crawler« which calculates welding processes in advance before carrying them out. Therefore, the robot uses the precise measurement values provided by the powerful laser profile scanner from Micro-Epsilon.
A scanCONTROL 2900 scanner is fixed on the Inrotech-Crawler and detects the geometry of the seam to be welded before the actual welding process starts. Only these high precision profile measurements enable the process to be automated. Due to its compact, lightweight design with integrated controller, the laser profile scanner is ideally suited to this measurement task.
Various connection possibilities offered by the SDK (Software Development Kit) enable the customer to directly transmit the profile data calibrated to their own software via scanCONTROL DLL. The Weldlogic technology from Inrotech then calculates, among other things, the number of welding passes, the position of the weld seams, the weld speed and the oscillation width. Directly after the calculation, the Crawler automatically performs the welding process.
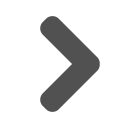 Compact laser scanner for high precision
|
|
|
Biaxial inspection of adhesive bonds
|
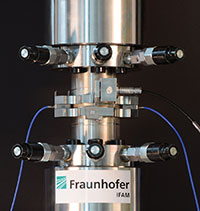 |
The layer thickness of the adhesive bond is typically only a few tenths of a millimeter. The sample is now loaded by tension (axial displacement) and/or torsion. Measuring these very small displacements requires a very accurate and stable measuring system. The test set-up therefore includes three MicroEpsilon capacitive sensors, which are connected via a capaNCDT 6500 capacitive controller with DL6530 demodulator module. Using a special holder, the sensors are attached directly to the tube joining parts of the double tube sample. Two flat sensors with 2 mm measuring range measure the displacement in the axial direction and a cylindrical sensor measures the displacement by torsion. Due to the non-contact measuring technique used, it is easy to decouple axial displacement components and the torsion-induced displacement.
|
|
|
Edge detection of fabric strips in the cutting machine
|
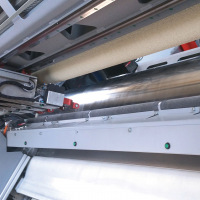 |
If the position of the material web is not recognized or is recognized incorrectly, this can result in waste from faulty cutting and machine malfunctions due to missing controller signals. Therefore, the optoCONTROL CLS-K-31 fiber optic sensor from Micro-Epsilon is used for position detection.
The sensor reliably detects the beginning of the roll. It is mounted directly on one of the cutting blades and recognizes from a distance of around 140 mm when the fabric is in the cutting position. A switching output (PNP) transmits a signal level directly to the controller and the cutting process begins. In this way, the cutting elements can be positioned exactly to 0.5 to 2 mm depending on the material. After each cut, the fabric position is recalculated. The measuring process is carried out at feed speeds of 20 m/min.
The optoCONTROL CLS-K-31 measuring system from Micro-Epsilon provides highly reliable and reproducible measurement results, which ultimately optimizes cutting accuracy, while reducing waste and process disruptions. The CLS-K-31 is even virtually insensitive to scratches and contamination on the shiny metallic surface of the roller.
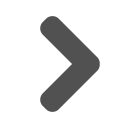 Fiber optic sensors for gap, diameter, edge and presence
|
|
|
Gap analysis in axial piston pumps
|
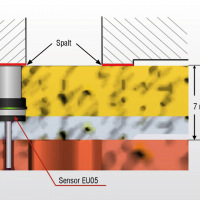 |
So far, gap measurements inside the pumps were not possible because of the extreme requirements. The sensors must be resistant to high speeds, high pressures up to 1,000 bar and temperatures above 100 °C. Furthermore, the pumps are extremely compact, which significantly limits the space available for integration of sensors. Thanks to the extremely small sensor designs and their high pressure and temperature stability, the eddyNCDT inductive miniature sensors are ideal for this application. The eddyNCDT 3300 eddy current measuring system, which is one of the most powerful systems in the world, is therefore used on the test rig for evaluating the pumps.
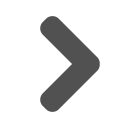 eddyNCDT 3300
|
|
|
Position measurement of the tailstock
|
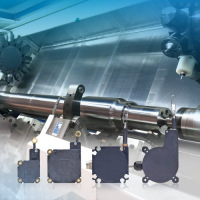 |
The tailstock is an important part of a lathe or milling machine. The tailstock is used to support long workpieces by means of a center, which catches in the center hole on the front side of the workpiece. In order to detect the center tip, compact draw-wire sensors from Micro-Epsilon are used. The measuring wire is connected to the center tip and measures the displacement of the tailstock.
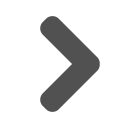 Draw-wire displacement sensors
|
|
|
Measuring tool holders in the magazine
|
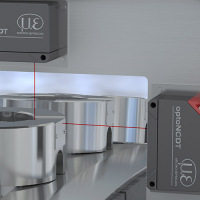 |
Modern machine tools have complex magazines with various tools that are automatically picked up by the machine. In order for these tools to be accurately picked up, the tool holders must be precisely positioned. To check the position of the tool holders, optoNCDT 1420 laser sensors are used, which measure the metallic holders from above and from the side. These smart laser sensors stand out due to their high measuring rates while providing precise measurement values, despite strongly reflecting, metallic surfaces.
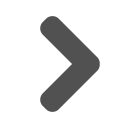 Smart laser triangulation displacement sensor
|
|
|
Nanometer positioning in lithography machines
|
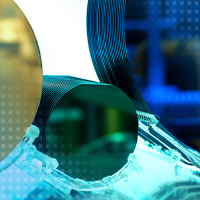 |
To illuminate individual components on the wafer, the lithographic devices move the wafer to the respective position. Capacitive displacement sensors measure the position of the travel path in order to enable nanometer-accurate positioning.
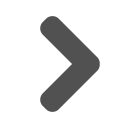 Capacitive displacement sensors and measurement systems
|
|
|
Measuring thermal length expansion of spindles
|
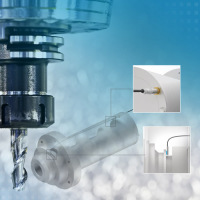 |
The SGS 4701 displacement measuring system (Spindle Growth System) is developed specifically for high speed milling machine applications. Due to high machining speeds and the heat generated, the linear thermal expansion of the spindle in the precision machine tool must to be compensated for in order to keep the tool in a defined position at all times.
The SGS sensor measures the thermal and centrifugal force expansion of the spindle. These measurement values are fed into the CNC machine tool as correction values, compensating for any positioning errors. The SGS 4701 operates on the eddy current measuring principle. This non-contact measurement method is wear-free. Furthermore, the measurement procedure is resistant to disturbances such as heat, dust and oil.
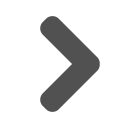 eddyNCDT SGS4701
|
|
|
Monitoring the clamping position of tools
|
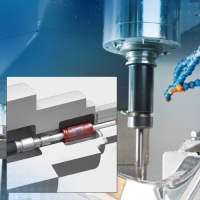 |
Often, initiators and switching rings, which provide a switching signal, are used to monitor the clamping position in high-performance tool machines. However, these require complex adjustment and set up. Analog sensors from the Micro-Epsilon LVP series offer significant improvements. The cylindrical sensor is integrated into the release device and directly measures the clamping stroke of the drawbar. On the drawbar, a ring is fastened, which acts as the target for the sensor. The LVP sensor can be universally used with the most varied types of tool due to an extremely compact sensor design. The sensor supplies an analog signal according to the stroke motion of the drawbar when clamping the tool. Consequently, continuous monitoring is possible without the switching point having to be laboriously set mechanically. The miniaturized sensor electronic unit can either be accommodated at the point of measurement or in the control cabinet. Thanks to its high accuracy, the LVP sensor contributes significantly to meeting the ever increasing demands on machine tool precision and availability.
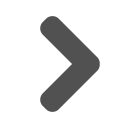 Inductive sensors for specific applications
|
|
|
Compensating for axial extension of milling spindles
|
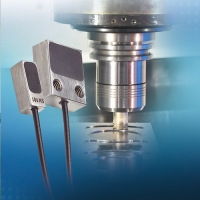 |
Due to high machining speeds and the heat generated, the linear thermal expansion in milling spindles needs to be compensated for in order to keep the tool in a defined position at all times. The SGS sensor developed by Micro-Epsilon measures the thermal and centrifugal force expansion of the spindle. As well as measuring linear thermal expansion, the temperature of the sensor is also detected and output.
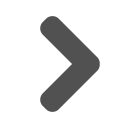 eddyNCDT SGS4701
|
|
|
Foreign body detection in medical technology
|
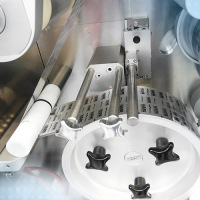 |
In this application, the MDS sensor recognizes foreign bodies in blister machines during the tablet packaging process. Via the movement of overhead touching rollers, foreign bodies between the blister packaging and covering material can be detected. Exceeding a pre-defined point triggers an alarm.
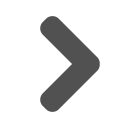 Magneto-inductive distance sensors
|
|
|
Valve lift measurement in the food industry
|
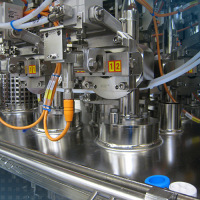 |
During the filling of drinks cartons, the exact dosage is a critical factor. The sensor measures the valve lift of the filling line and requests several switching points in a measuring range of 35mm. The sealed stainless steel housings of the MDS-45-Mxx series are ideal for the food industry.
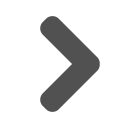 Magneto-inductive distance sensors
|
|
|
Monitoring embossment depth
|
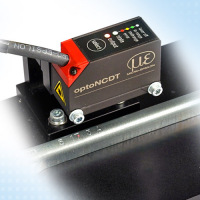 |
In embossing machines, car body IDs are punched into the vehicle frame. The embossment depth must be in a defined tolerance range. In order to position the embossing tool, laser triangulation sensors from Micro-Epsilon detect the distance between the embossing tool and the component. After the embossment is finished, the sensor measures the profile of the embossment and ensures that all characters are embossed to the required depth.
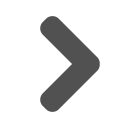 Smart laser triangulation displacement sensor
|
|
|
Monitoring oil gaps in hydrostatic bearings
|
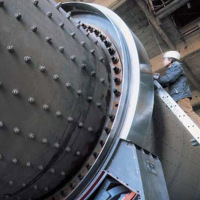 |
Hydrostatic bearings are used in large plant and machinery such as stone mills, telescopic installations etc. Monitoring the gap size is a critical factor, as any disturbances in the hydraulics can cause pressure drops, which in extreme cases, can cause the gap to close, resulting in damage to the bearings and ultimately system failure. Here, it is important to have a system that is easy to install as also ageing plants have to be retrofitted. Due to the long service life and the worldwide use of this plant, the sensor should be easy to replace. For this reason, non-contact eddy current displacement sensors of the eddyNCDT 3001 series are used.
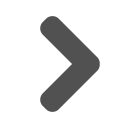 eddyNCDT 3001
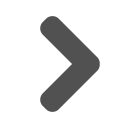 Inductive sensors (eddy current) for displacement, distance & position
|
|
|
Web-edge detection in the calender of a paper machine
|
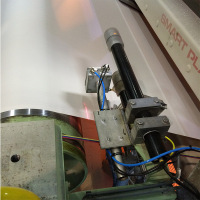 |
If movement of the paper web in the calender is not exactly executed in one line, the heated calender roller is pressed directly onto the coating of the opposite roller, which can damage it. Repairing this special coating or even replacing the whole roller would be very costly, which is why it is mandatory to control the position of the web edge. This is where laser line sensors from Micro-Epsilon are utilized, transferring the exact position of the web edge directly to the machine control system.
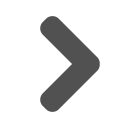 Laser scanners for 2D/3D profile measurements
|
|
|
Temperature measurement for injection mould applications
|
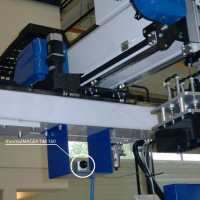 |
Users of injection molding machines for plastics processing are facing increased quality requirements imposed by end-users, in particular for automotive applications. Because of this trend, the importance of inline temperature control right after extrusion as a global quality attribute is growing.
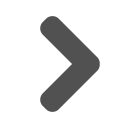 Thermal imaging cameras for industrial temperature monitoring
|
|
|
Active compensation for movements in the measurement process
|
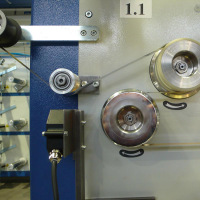 |
Harsh industrial environments place high demands on optical displacement sensors – precise measurements must still be possible despite dust and high processing speeds. The optoNCDT 1750 and optoNCDT 2300 series of laser sensors have overcome these challenges for many years. However, if motion disturbances (e.g. belt movements, radial movements of pulleys, and base body vibrations) occur that are greater than the object being measured, the measurement process may be impeded or made impossible, for example folds in a belt.
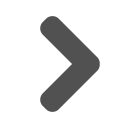 Universal laser sensor for industry & automation
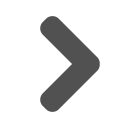 Most Advanced Laser Displacement Sensor
|
|
|
Fluid level measurement of aluminum pig irons
|
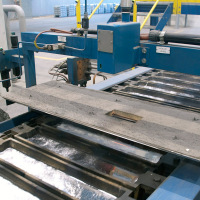 |
In aluminum casting plants or foundries, the cast is poured into shape to form small bars, known as pig irons. The charging level in the forming process is critical in ensuring consistent weight of the pigs. Using a special non-contact measuring device, the depth of fill is recorded. For these applications, an Austrian system builder uses laser scanners.
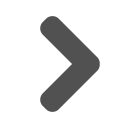 Laser scanners for 2D/3D profile measurements
|
|
|
Measurement of the radial deviation of a cutter disk
|
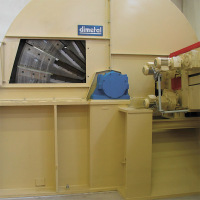 |
During the manufacture of veneer strips from laminated wood, the precision of the cutting disk determines the quality of the final product. High demands are placed on the veneer strips in terms of dimensional conformance. The thickness of the strips must be less than 1 mm and may only have tolerances in the micrometer range. In order to comply with the quality criteria, the radial deviation of the cutting disk is measured and monitored during the production process using a non-contact optoNCDT 2300 laser triangulation sensor. This means that high demands are placed on the measuring system: Dust, chippings and a shiny target surface must not affect the measurement accuracy. The cutting disk has a diameter of 3200 mm and is equipped with 24 knives. The rotation speed is 180 to 210 rpm.
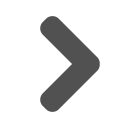 optoNCDT Laser Sensoren
|
|
|
Position checking on robots
|
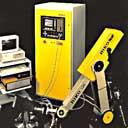 |
The introduction of the international standard ISO 9283 demands new non-contacting measurement methods. The measurement system for the position measurement is composed of a measurement cube with a defined weight, a sensor and a support. The sensor is equipped with six U15 eddy current sensors. During the measurement the robot moves the measurement cube into the sensor range. The data from the eddy current sensors is passed via a fast interface to the PC where it is processed. Measurement inaccuracies due to linearity and tilting errors (parallelism between the sensor and measurement object) and thermal effects are additionally compensated in the measurement software.
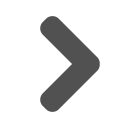 Inductive sensors (eddy current) for displacement, distance & position
|
|
|
Exact crusher gap adjustment in rotary crushers
|
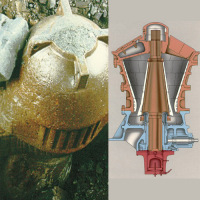 |
Rotary crushers for quarries or ore mines can grind up to 3500 t of material to the desired grain size in one hour. For this purpose an eccentric bearing bush generates a rotary-oscillating movement of the crusher axle, thereby constantly changing the gap between the crusher jaws and the crushing cone. For grinding the set gap continuously moves along the inside perimeter of the crushing room. With a longdistance sensor in the hydraulic cylinder the crushing gap can be exactly adjusted by raising and lowering the axle.
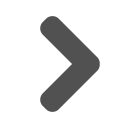 induSENSOR EDS
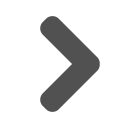 Inductive sensors (LVDT) and gauges
|
|
|
Non-contact thickness measurement of aluminum
|
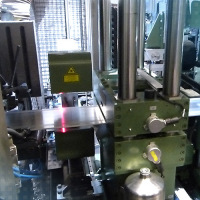 |
For the prompt detection of incorrect thickness of aluminum strips, optoNCDT laser triangulation sensors are used as modern alternative solution to isotopic measuring systems. At the measurement location, the sensors are mounted opposite to each other, above and below the conveyed aluminum strip. Regardless of the exact height position of the strip, the sensors provide the exact material thickness based on a simple distance signal coupling, F=Ref. - (A + B).
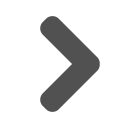 optoNCDT Laser Sensoren
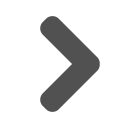 Measuring and inspection systems for the metal processing industry
|
|
|
Flatness measurement in rolling mills
|
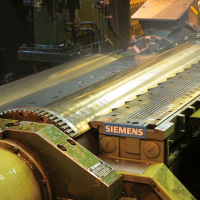 |
The requirements on the surface quality of rolled sheet metal are continually increasing. This may be steel sheet which is used, for example, for stainless steel fronts in kitchens, or also aluminum sheet used in the automotive field. The surface must be flawless to offer the customer a high quality visual appearance. Consequently, measurement equipment is employed in rolling mills to acquire the so-called flatness of the rolled sheet metal. Flatness is taken to mean the surface evenness of the sheet in the unstressed state.
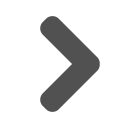 Inductive sensors (eddy current) for displacement, distance & position
|
|
|
Yarn thickness
|
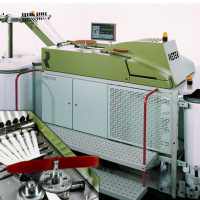 |
A consistent yarn thickness is a prerequisite in the textile industry for high quality products. Therefore, the naturally occurring yarn thickness fluctuations must be eliminated. The yarn is drawn to a constant thickness using a stretching tool. The measured data for controlling the stretching tool are provided by an eddy current sensor which indirectly measures the thickness. The thickness is transmitted to the eddy current sensor using sensing rollers. After the stretching, the result of the processing operation is also checked by an eddy current sensor.
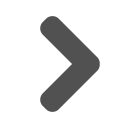 Inductive sensors (eddy current) for displacement, distance & position
|
|
|
|