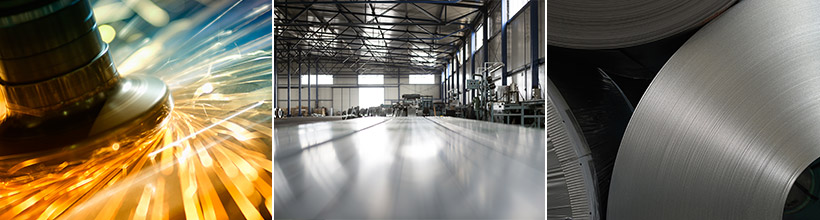 |
|
Metal production and processing
|
Intelligent sensors are required in production, processing, conveyance and storage of metallic materials. There, sensors enable efficient and safe production and later failure-free processing. Micro-Epsilon has expertise and know-how in a wide range of applications: in the positioning of cranes, machine parts and materials, in the monitoring of the thickness of metal strips and slabs to the profile measurement of pressed moldings. |
|
Optimizing weld seams with profile measurements
|
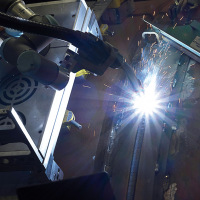 |
Inrotech A/S in Denmark relies on sensors from Micro-Epsilon to achieve optimal quality of weld seams in a fully automatic process. The company has developed a welding robot called »Inrotech-Crawler« which calculates welding processes in advance before carrying them out. Therefore, the robot uses the precise measurement values provided by the powerful laser profile scanner from Micro-Epsilon. A scanCONTROL 2900 scanner is fixed on the Inrotech-Crawler and detects the geometry of the seam to be welded before the actual welding process starts. Only these high precision profile measurements enable the process to be automated. Due to its compact, lightweight design with integrated controller, the laser profile scanner is ideally suited to this measurement task. Various connection possibilities offered by the SDK (Software Development Kit) enable the customer to directly transmit the profile data calibrated to their own software via scanCONTROL DLL. The Weldlogic technology from Inrotech then calculates, among other things, the number of welding passes, the position of the weld seams, the weld speed and the oscillation width. Directly after the calculation, the Crawler automatically performs the welding process.
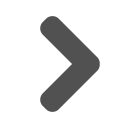 Compact laser scanner for high precision
|
|
|
3D measurement of components prior to plasma cutting
|
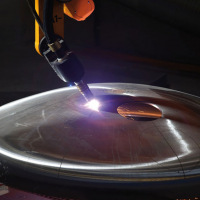 |
In order to process these huge domes quickly, fully automatically and at extreme precision, it is necessary to determine their shape and exact position within the production line. As the pure CAD data of the dome often differs by several centimeters from the actual dimensions, the 3D profile of the covers is measured before processing using scanCONTROL 2900 laser scanners. The exact dimensions are then determined from the 2D data generated by the scanner which is connected to a 6D scanner position system. The scanning process is performed at high speeds up to 60 m/min. Therefore, a reliable hardware trigger is required to obtain the real shape of the target. Its compact design, integrated electronics and speed make the MicroEpsilon laser scanner suitable for inline integration. In addition, high performance scanners achieve a high repeatability of 50 µm/m even with different reflective properties of the metallic test objects.
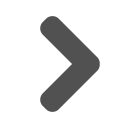 Laser scanners for 2D/3D profile measurements
|
|
|
Bending/smoothness of aluminum cast covers
|
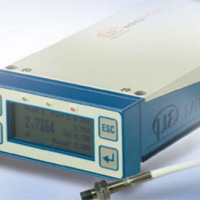 |
After AL covers have been cast and prior to milling of the sealing surface the covers must be manually straightened and sorted into OK/NOK. This operation takes place in a rough environment (casting bay). The measuring technique that was used earlier (probes) are subject to a high degree of wear and had to be replaced in regular intervals. In order to minimize spare parts costs the customers have decided in favor of the non- contacting and non-wearing eddy-current measuring system. What is of special importance for the success of this measuring method is the fact that eddyNCDT eddy-current sensors, due to the possibility of 3-point-linearization, supply reliable measuring values even with complex target geometries.
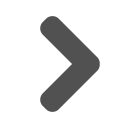 eddyNCDT 3300
|
|
|
Monitoring mold deformations in aluminum die-casting
|
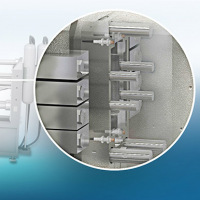 |
Monitoring tool deformation using inductive sensors based on eddy current enables high product quality combined with improved tool life and reduced rework. Usually, three to four eddyNCDT 3005 eddy current systems are used to ensure consistent gap monitoring. A system consists of a compact and robust controller, which together with the cable and sensor form a solid unit. The integrated system design increases robustness and resistance to external factors, making the system insensitive to harsh industrial environments with high temperatures, dust, dirt or pressure, and delivers accurate results regardless of the environment. Due to the compactness of the eddyNCDT 3005 system, subsequent integration into an existing machine is possible at any time.
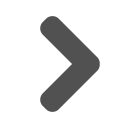 Compact, inductive displacement measuring system for serial applications
|
|
|
Monitoring metal sheet infeed during the pressing process
|
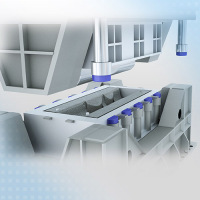 |
The measurement of the distortion is carried out using several optoNCDT 1420 laser triangulation sensors, which are placed around the metal sheet, either in the tool or on the side of the tool. The arrangement is chosen in such a way that the laser beam measures on the edges of the sheet, which is between the top and bottom of the tool. Due to the extremely small measurement spot size, the laser is therefore able to measure extremely small gaps between the two tool parts of less than one millimeter. The measured values are transmitted via analog or digitally to the controller. They allow a conclusion to be drawn on how much material has flowed. This enables, for example, the pressing force to be controlled during the ongoing process, reducing waste, material consumption, downtime and costs. Micro-Epsilon laser triangulation sensors are rugged and can withstand high mechanical loads such as vibration and shock.
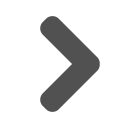 Smart laser triangulation displacement sensor
|
|
|
Coil diameter
|
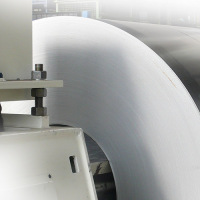 |
Rolled strips in the metal industry are wound on coils for transport. For the later processing when the coils are unwound, it is important to know how much material has already been unrolled. This task is simple to solve by using an optoNCDT ILR optical length sensor. It continuously measures onto the surface of the coil and thus records the diameter. The diameter of the coil reduces due to the unwinding which is measured using the increase in distance from the coil surface to the sensor. Using the coil thickness, the material length can be recalculated using specific algorithms.
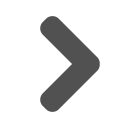 Laser distance sensors for extra long ranges
|
|
|
Coil unwinding
|
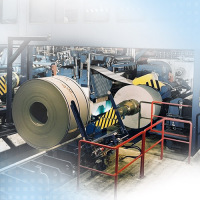 |
Rolled strips in the metal industry are wound on coils for transport. For the later processing when the coils are unwound, it is important to know how much material has already been unrolled. This task is simple to solve by using an optoNCDT ILR optical length sensor. It continuously measures the distance from the surface of the coil to the center. The thickness of the coil reduces due to the unwinding which is measured using the increase in distance from the coil surface to the sensor. Using the coil thickness, the material length can be recalculated using specific algorithms.
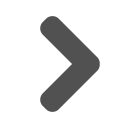 Laser distance sensors for extra long ranges
|
|
|
Measuring and inspecting laser welding seams
|
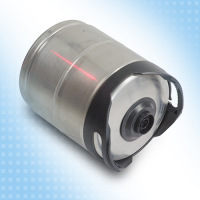 |
Fully automatic welding units can be found in numerous industrial areas. Quality control in the form of a 100% inspection is indispensable in order to achieve defect-free weld seams. Laser profile sensors from Micro-Epsilon monitor the weld seam and immediately detect defects as well as the completeness of the width and height profile of the weld.
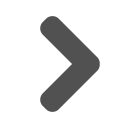 Laser scanners for 2D/3D profile measurements
|
|
|
Double sheet detection before pressing
|
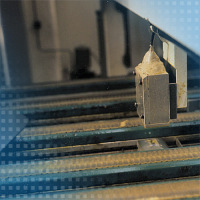 |
Before shaped sheets are fed into the press, laser-optical displacement sensors are used, which enable double sheet detection. Two sensors are mounted above and below the continuous sheets and provide a thickness value regardless of the exact position of the sheets.
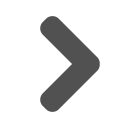 Extreme dynamic laser sensor with anti speckle feature
|
|
|
Thickness measurement of metal strips
|
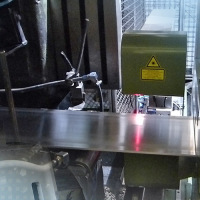 |
When measuring the thickness of metal strips, optical methods based on laser triangulation have numerous advantages compared with other methods. They measure without contact and therefore without wear. Moreover, independently of the condition of the material it is possible to carry out an exact geometrical measurement in relation to the strip surface. Micro-Epsilon offers robust measuring systems as C-frames and O-frames which operate independently of the alloy.
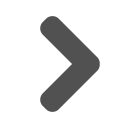 Measuring and inspection systems for the metal processing industry
|
|
|
Measurement of the zinc strip color in the production plant
|
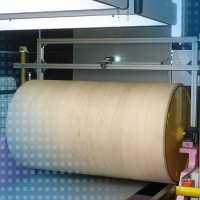 |
In the production of high-quality material strips and boards made out of titanium zinc, the surfaces receive specific treatment. Therefore, the coloring of the zinc products is already determined during the production process.
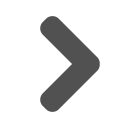 High Speed Photospectrometer colorCONTROL ACS7000
|
|
|
Weld seam inspection on pipes
|
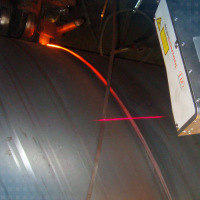 |
A perfect weld seam is essential in a leak tight pipe. scanCONTROL laser scanners are therefore used during spiral welding to align the weld flanks. This results in a much more reliable welding process. The long base distance of 600mm and the protective housing for the sensor are also important here.
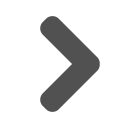 Laser scanners for 2D/3D profile measurements
|
|
|
Acquisition of the internal diameter of tubes
|
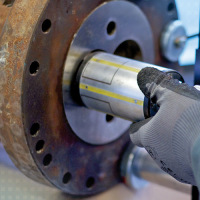 |
An important criterion for the quality or the wear of tubes in industrial applications is the dimensional conformance of the internal diameter over the complete length. Where high demands are made on accuracy, a quick and reliable recording of the data must be ensured, because, for example, wear measurements must be carried out in the chemical industry on pipes which are already installed, i.e. with the plant shut down. Two pairs of sensors record two tracks offset by 90° in one measurement step.
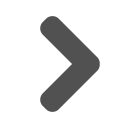 Non-contact inspection of extruder bores
|
|
|
Strip width when trimming metal strips
|
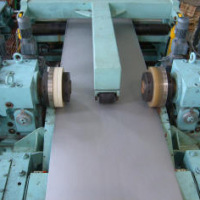 |
As different widths are frequently required during the production of metal strips, the strips must be trimmed after the rolling process and both the cutters must be movable electrically. The distance is now measured by difference measurement using laser sensors from Micro-Epsilon so that compliance with the target dimensions no longer has to be checked manually as was the case previously. Two optoNCDT sensors are used for this.
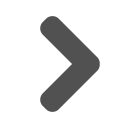 optoNCDT Laser Sensoren
|
|
|
Weld seam tracking for pipeline inspection
|
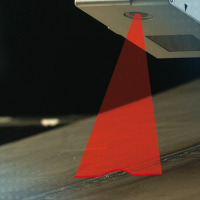 |
Defective weld seams are often the reason for leaks on pipelines. Therefore, the seams are inspected on the outside after the welding with the profile scanner scanCONTROL. In doing so, the scanner is positioned in a testing device on the pipe. After the manual alignment, the scanner automatically inspects the weld seam and centers itself automatically on the pipe in doing so.
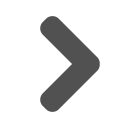 Laser scanners for 2D/3D profile measurements
|
|
|
High precision pipe measurement
|
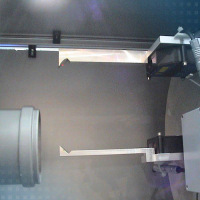 |
High precision pipe measurement Pipes, fittings and sleeves are inspected using random sampling for their dimensional accuracy in a special system. Sensors of the optoNCDT 1700 series rotate mounted on a plate. The laser beam is deflected by 90° by an adjustable mirror for the measurement. The system produces a detailed thickness profile of the target using the difference method.
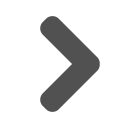 optoNCDT Laser Sensoren
|
|
|
Aluminum rim dimension
|
 |
Maximum quality is required for the production of aluminum rims so that the necessary smooth running is achieved in the subsequent use. In contrast to tactile methods, laser scanners from the Micro Epsilon scanCONTROL series are used for this. These sensors inspect the rims for all geometric defects in an integrated tester. Therefore, a 100% in-line quality control is achieved.
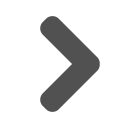 Laser scanners for 2D/3D profile measurements
|
|
|
Roller clearance
|
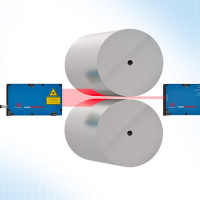 |
The distance of both rollers from each other or from the roller to the support surface is the crucial dimension for rolling processes for metals, plastics or other materials. In the case of sensitive processes and high material accuracies, the clearance must be checked constantly so that imminent rejection is avoided. The contacting inductive and the non-contact methods are suitable for this. In the case of contacting methods, the sensor is mounted on the outside on the roller guide. The change in clearance is transmitted to a plunger whose position change is measured by the inductive sensor. In the case of the non-contact method, the roller is between the transmitter and receiver of an optical micrometer. The emitted light curtain is partially covered by the roller. The remainder reaches the receiver through the gap. The gap can be calculated based on the light quantity measurement.
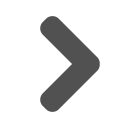 High resolution optical micrometer
|
|
|
Coil edge
|
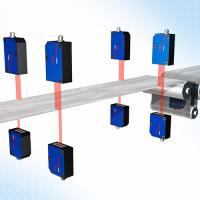 |
Rolled sheets in the metal industry are wound on coils for transport. It is important that directly before and also after the coiling, to check the position and the edge condition of the metal strip. optoCONTROL optical micrometers are used for this. If the edge of the coil is within the measuring range during the winding or unwinding, the position and the edge structure can be determined from this. This technique ensures that the coil is wound correctly and also that the correct metal strip quality has been delivered for the unwinding.
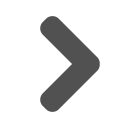 High resolution optical micrometer
|
|
|
Tempering - temperature measurement
|
|
|
Temperature measurement of molten metal
|
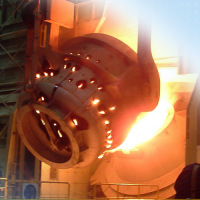 |
Temperature monitoring of liquid metal is important to maintain the corresponding process temperature during casting. With the thermoIMAGER TIM M05, Micro-Epsilon offers the right spectral range as well as a continuous measuring range of from 900 °C to 2000 °C. Due to the high frame rate of 1 kHz and the high optical resolution, thermal images can be recorded quickly and reliably.
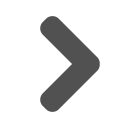 Infrared sensors and thermal imagers for precise temperature measurement
|
|
|
Temperature measurement in the hot rolling mill
|
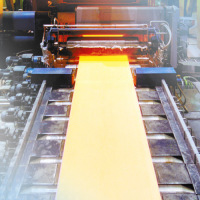 |
In the milling line, the forming temperature between the individual rolls is measured continuously. Micro-Epsilon's non-contact infrared pyrometers measure with a short response time and from a safe distance. For the different metals and temperature ranges, IR temperature sensors and thermal cameras with different wavelengths are available.
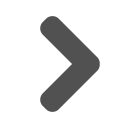 Infrared sensors and thermal imagers for precise temperature measurement
|
|
|
Weld seam profile
|
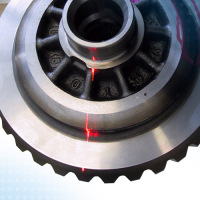 |
Welding robots which perform the joining automatically are often used for joining metals. For visible parts, the weld seam must satisfy certain optical criteria; for example, there must be no remaining welding beads. A laser scanner is installed directly after the welding head for this. It measures all the weld seams made and arranges for the robot to make corrections if necessary.
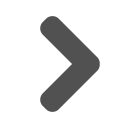 Laser scanners for 2D/3D profile measurements
|
|
|
Aluminum thickness
|
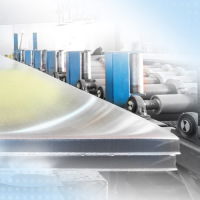 |
It is important to know the thickness of the plates for the manufacture of aluminum plates. The non-contact profile measuring system measures the profile of the plates using a capacitive sensor. At the same time, the width of the plate is determined during the measurement. The reversing rolling stand and the following roller stands can be better adjusted using the data obtained. The system is integrated in the existing roller track. Installed directly before the cropping shear where the plate is stationary for the cut, the production process is not impaired.
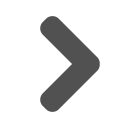 Inspection systems for inline quality control
|
|
|
|