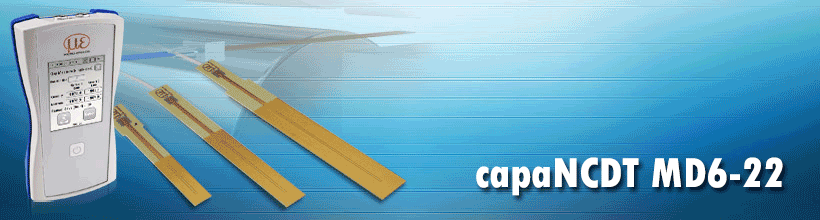 |
|
Capacitive mobile gap measurement with high precision Product Technology
|
|
|
|
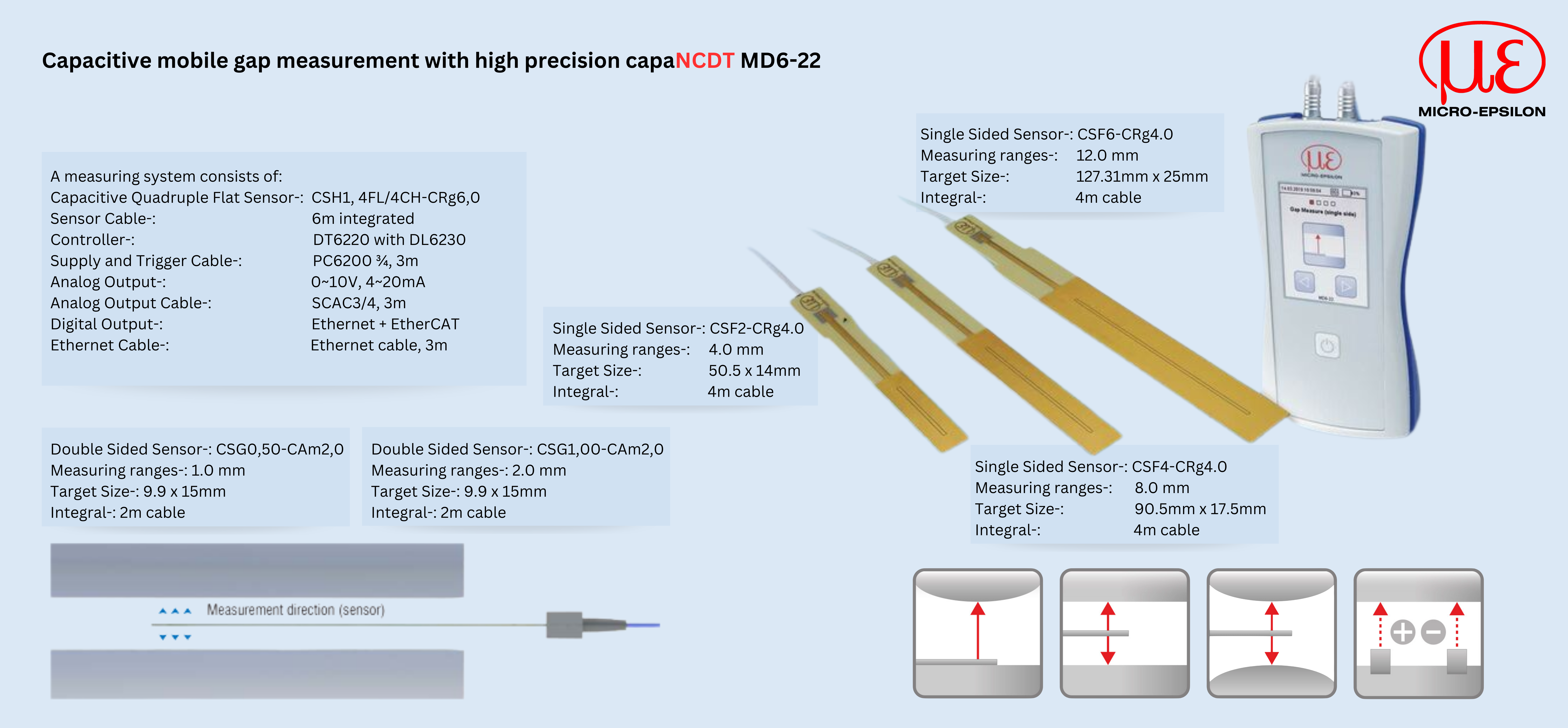 |
|
The capaNCDT MD6-22 capacitive dual-channel handheld gauge is used for mobile and precise measurement of gaps. This measuring device impresses with high accuracy, intuitive operation and long battery life. Thanks to preset measurement modes, the handheld gauge is immediately ready for use. Compatible with all capacitive sensors from Micro-Epsilon, the MD6-22 is used in different measurement tasks, e.g. for rotor gap monitoring in wind turbines and alignment of rollers in plant and machinery. |
|
|
|
Intuitive operation & immediately ready for use
Preset measurement modes make the capaNCDT MD6-22 immediately ready for use. The measurement types are matched to the different sensor types and targets:
|
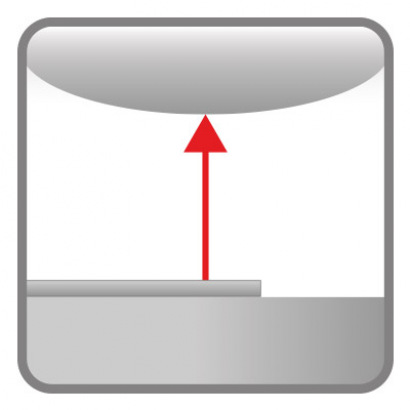 |
|
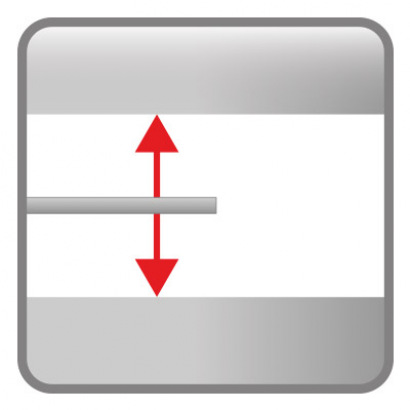 |
|
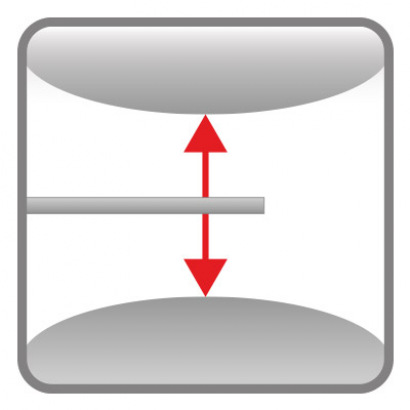 |
|
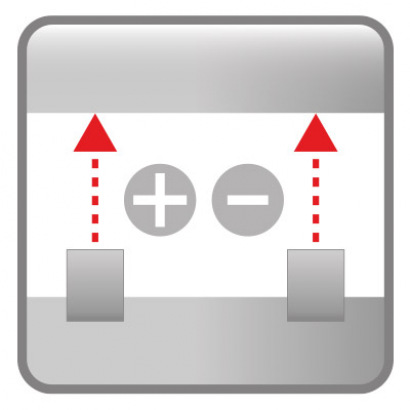 |
Single-sided gap measurement on curved surfaces
|
|
Double-sided gap measurement on flat surfaces with compensation of the sensor alignment |
|
Double-sided gap measurement on curved surfaces
|
|
Signal evaluation of two sensors measuring one side
|
|
|
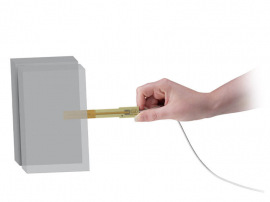 |
|
Mobile gap measurement at the highest precision
Inserted into the gap, the flat sensors from Micro-Epsilon determine the gap width based on the active measuring area. Gaps up to 12 mm can be detected reliably.
|
|
|
|
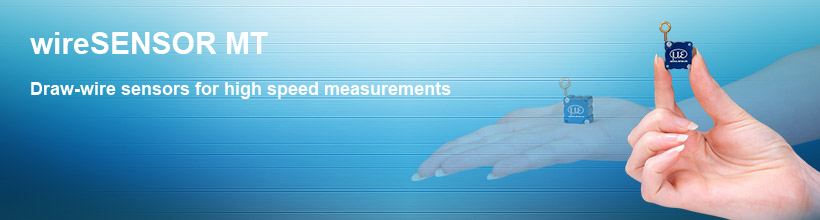 |
|
optoNCDT 1220
|
|
Characteristics
Measuring range (mm): 40 | 80 | 130
Linearity ±0.4% FSO
Output types: potentiometer
Easy and flexible mounting
For fast accelerations up to 60 g
Smallest design worldwide
|
|
Miniature draw-wire sensors – wireSENSOR MT
Miniature MT draw-wire sensors are the smallest draw-wire sensors worldwide. They are designed specifically for test applications where high wire accelerations occur such as crash tests. Their miniature design enables installation into very small spaces. Through-bores in the housing support easy, fast mounting..
|
|
|
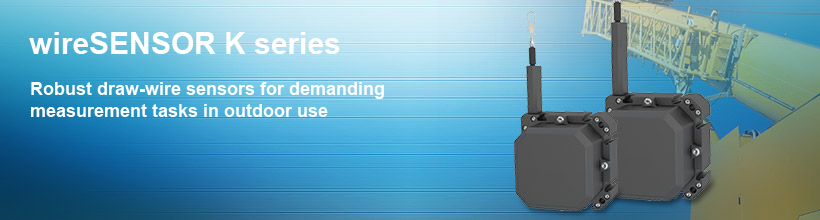 |
|
optoNCDT 1220
|
|
Characteristics
Measuring ranges: 2.3 m to 5 m
Linearity: ≤ ± 0.2 % FSO
Outputs: analog (U/I), potentiometer
Robust plastic housing
Durable sensor design
Compact housing allows flexible integration
Quick and low cost OEM customization
|
|
Draw-wire K series sensors are designed for industrial serial applications in indoor and outdoor use. Their compact and robust housing made from glass-fiber reinforced plastic and their durable sensor design with separate drum and spring spaces offer increased protection against environmental influences. Their modular sensor design enables fast and low cost OEM customization. Specially in outdoor use, these sensors can be optimally adapted to the respective application. Draw-wire K series sensors are used in mobile machines, cranes and lifting technology..
|
|
|
|
|
Compact laser sensors for OEM and serial applications Product Technology
|
|
|
|
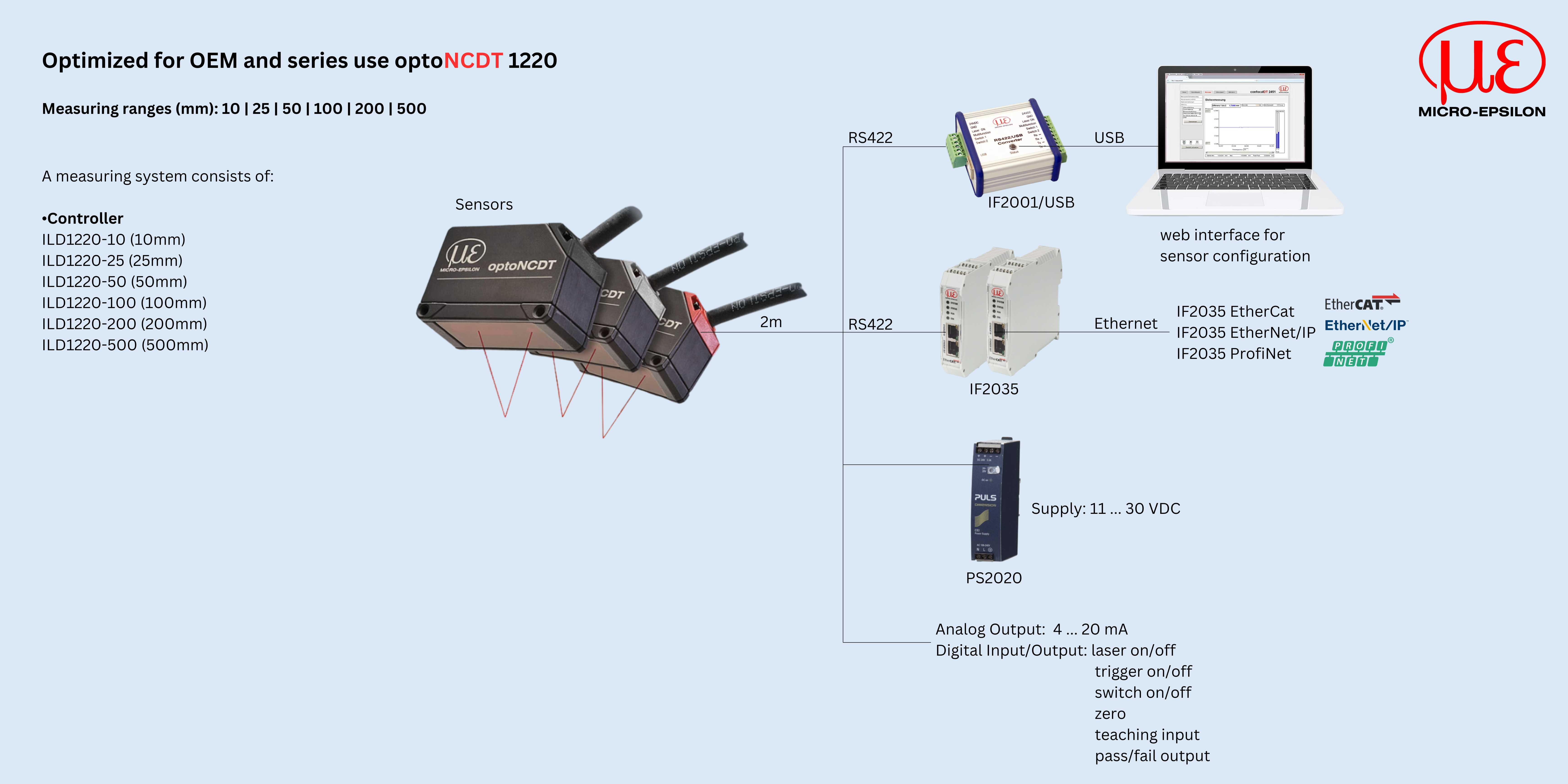 |
|
The optoNCDT 1220 is the entry-level model for precise measurements in industrial automation. This compact laser triangulation sensor measures displacement, distance and position with high precision. Based on an excellent price/performance ratio, this sensor is ideally suited to measurement tasks involving a large number of pieces. Therefore, the sensor can be used in all fields of automation technology, e.g., in machine building, 3D printers or robotics. |
|
|
|
|
|
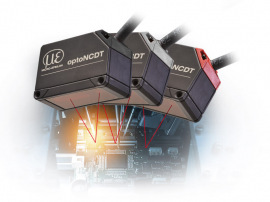 |
|
Ideal for automation and OEM integration
The optoNCDT 1220 laser sensor offers a unique combination of compact design, versatility and measurement accuracy which is exceptional in this sensor class. Its high repeatability and an adjustable measuring rate of 1 kHz make the laser sensor ideally suited to precise measurements. The Active Surface Compensation (ASC) provides stable distance signal control regardless of target color or brightness.
|
|
|
Easy integration
This compact sensor has an integrated controller. Therefore, no external controller devices are required. This enables the sensor to be integrated into restricted installation space. Its low weight makes the laser sensor ideally suited to applications where high accelerations occur. Due to its excellent price/performance ratio, the sensor is ideal for automation tasks and OEM integration with a large number of pieces.
|
|
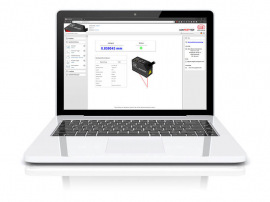 |
|
|
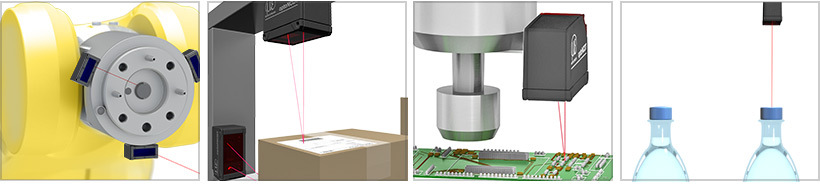 |
Ideal for distance control and position monitoring
The optoNCDT 1220 sensors are preferably used in applications that require high speed. Particularly with distance control tasks in industrial printers, robots and logistics processes, as well as the monitoring of packaging machines, these laser sensors impress with their high performance and compactness.
|
|
|
|
|
|
Confocal chromatic sensors for displacement, distance, position and thickness
Details
confocalDT IFS2404 displacement sensors are designed for high precision applications in restricted installation space. Based on a special lens technology, these sensors provide high resolution and a small light spot diameter. They are ideally suitable for high volume applications.
Measuring ranges (mm): 2
Linearity max. 1µm
Resolution 0.040µm
Distance and one-sided thickness measurement
|
|
|
|