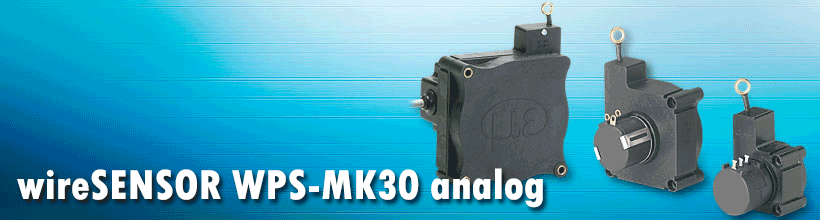 |
|
Draw-wire sensors for integration & OEM
|
|
MK series miniature draw-wire sensors are specially designed for serial applications with large numbers of pieces. The user benefits from a low price and compact sensor dimensions, therefore gaining new potential in design and cost optimization. As well as analog versions with potentiometer, current or voltage output, digital versions with incremental or absolute encoders are available. |
|
|
|
Robust draw-wire sensors – wireSENSOR WPS-MK30 analog
|
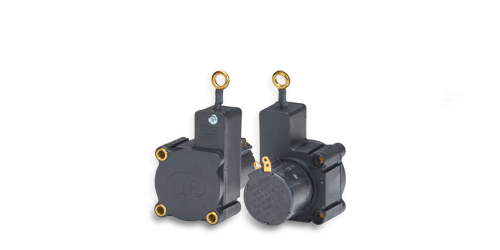
The miniature draw-wire sensors of the MK series are specially designed for use in high-volume production. Due to the favorable price and the compact size of the sensor, new potential designs and cost optimization are the benefits to the user.
|
|
|
|
|
Robust draw-wire sensors – wireSENSOR WPS-MK30 digital
|
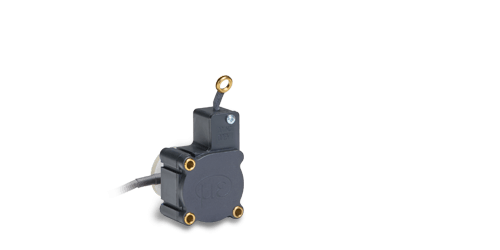
The miniature draw-wire sensors of the MK series are specially designed for use in high-volume production. Due to the favorable price and the compact size of the sensor, new potential designs and cost optimization are the benefits to the user.
|
|
|
|
|
Robust draw-wire sensors – wireSENSOR WPS-MK46 analog
|
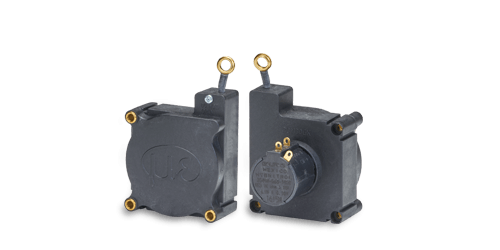
The miniature draw-wire sensors of the MK series are specially designed for use in high-volume production. Due to the favorable price and the compact size of the sensor, new potential designs and cost optimization are the benefits to the user.
|
|
|
|
|
Robust draw-wire sensors – wireSENSOR WPS-MK46 digital
|
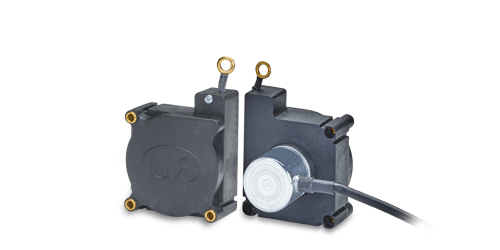
The miniature draw-wire sensors of the MK series are specially designed for use in high-volume production. Due to the favorable price and the compact size of the sensor, new potential designs and cost optimization are the benefits to the user.
|
|
|
|
|
Robust draw-wire sensors – wireSENSOR WPS-MK60 analog
|
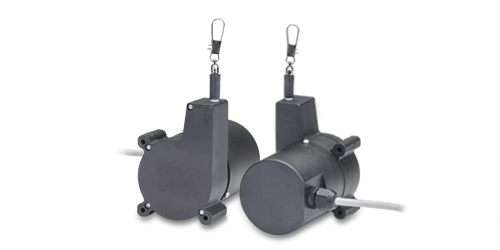
The miniature draw-wire sensors of the MK series are specially designed for use in high-volume production. Due to the favorable price and the compact size of the sensor, new potential designs and cost optimization are the benefits to the user.
|
|
|
|
|
Robust draw-wire sensors – wireSENSOR WPS-MK60 digital
|
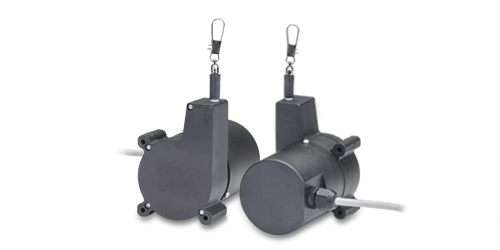
The miniature draw-wire sensors of the MK series are specially designed for use in high-volume production. Due to the favorable price and the compact size of the sensor, new potential designs and cost optimization are the benefits to the user.
|
|
|
|
|
Robust draw-wire sensors – wireSENSOR WPS-MK77 analog
|
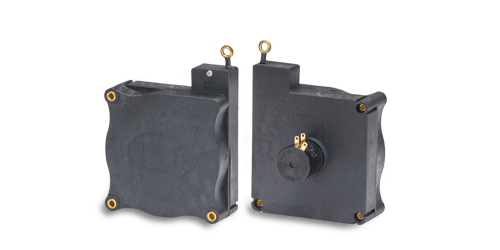
The miniature draw-wire sensors of the MK series are specially designed for use in high-volume production. Due to the favorable price and the compact size of the sensor, new potential designs and cost optimization are the benefits to the user.
|
|
|
|
|
Robust draw-wire sensors – wireSENSOR WPS-MK77 digital
|
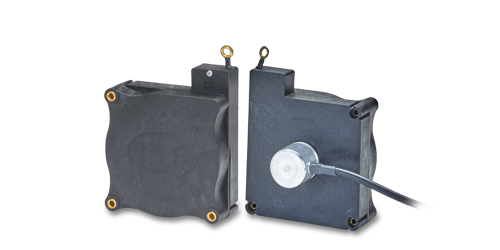
The miniature draw-wire sensors of the MK series are specially designed for use in high-volume production. Due to the favorable price and the compact size of the sensor, new potential designs and cost optimization are the benefits to the user.
|
|
|
|
|
Robust draw-wire sensors – wireSENSOR WPS-MK88 analog
|
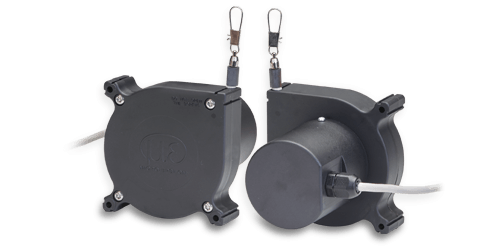
The MK88 is especially designed for mobile applications in series such as mobile cranes or mobile working platforms. The combination of dimensions, robust design, measurement range and price-ratio makes the MK88 unique. Therefore, it has the potential to reduce production costs significantly.
|
|
|
|
|
Robust draw-wire displacement sensors – wireSENSOR WPS-MK88-U45R
|
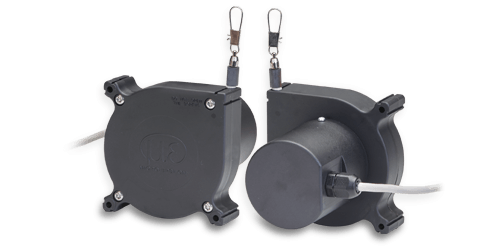
Similar to the MK88, the MK88-U45R draw-wire sensor is specially designed for high volume, mobile applications such as mobile cranes and elevating work platforms. The combination of its size, robustness and price makes the MK88 series unique, offering new potentials in design and cost optimization. Furthermore, the MK-88-U45R offers a distinct advantage in terms of service life due to its non-contact potentiometer. Its service life is eight times longer than sensors equipped with conventional potentiometers.
|
|
|
|
|
Robust draw-wire sensors – wireSENSOR WPS-MK120 analog
|
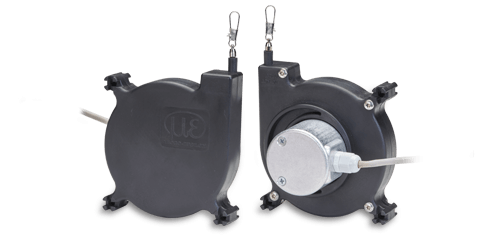
The miniature draw-wire sensors of the MK series are specially designed for use in high-volume production. Due to the favorable price and the compact size of the sensor, new potential designs and cost optimization are the benefits to the user.
|
|
|
|
|
|
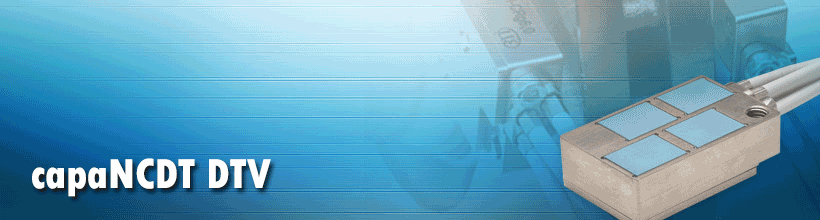 |
|
|
|
|
|
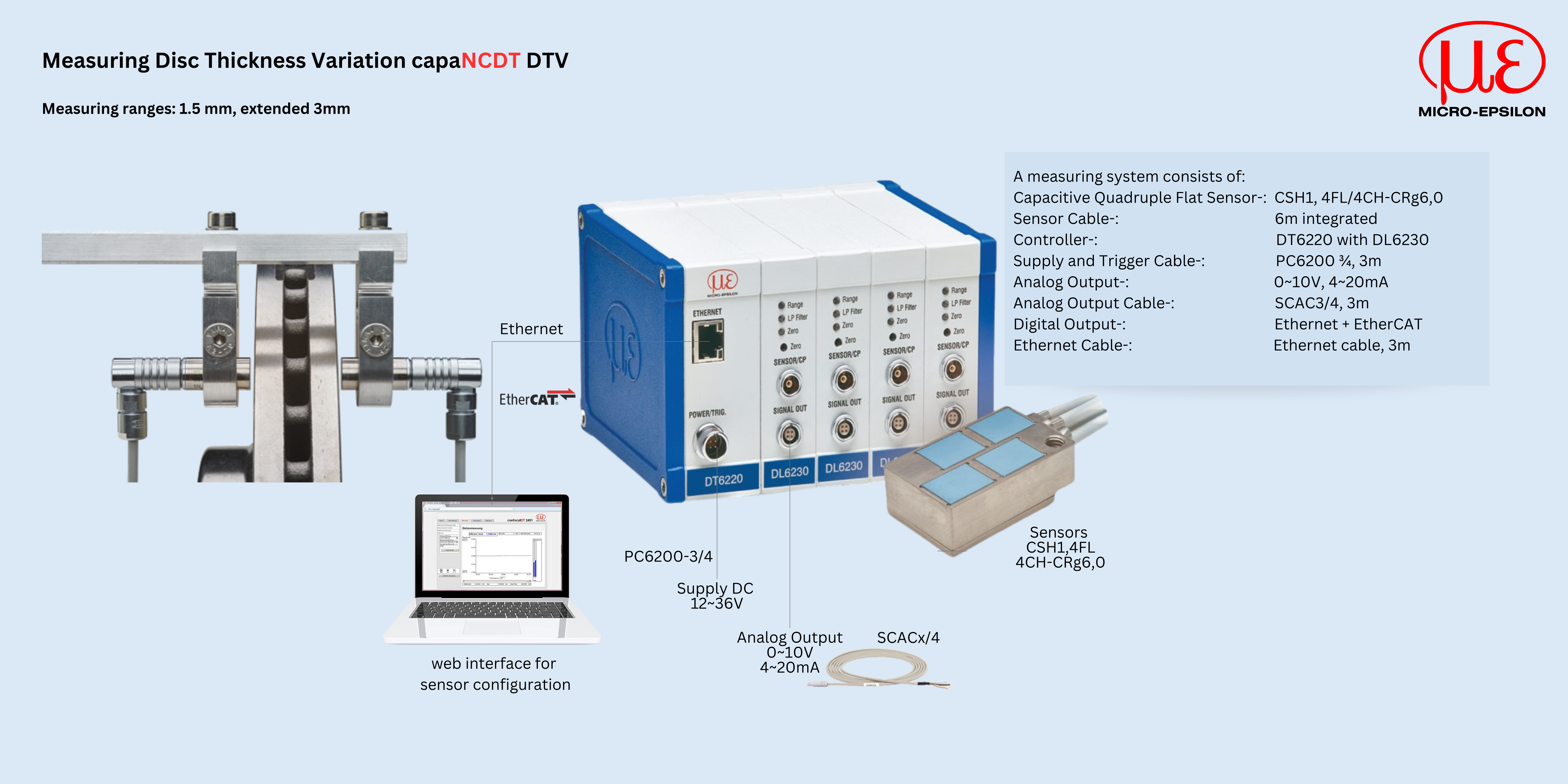 |
|
The capaNCDT DTV series is designed for non-contact detection of Disc Thickness Variation (DTV). Capacitive sensors for multi-track measurements and a carrying case including the complete measurement channel for mobile use are available. With the capaNCDT DTV measurement system, capacitive displacement sensors determine the thickness of the brake discs from both sides based on the difference principle. While the brake disc rotates, the thickness deviation is determined via the circumference of the entire disc. Using several sensors in pairs or the CSH1,4FL multi-channel sensor makes multi-track thickness measurement possible. Thickness measurements can be carried out in test benches, in road tests or in car repair shops. The DTV case is intended for mobile use, e.g., for quality assurance purposes and warranty claims. |
|
|
|
Robust multi-channel sensor for test benches and road tests
The innovative CSH1, 4FL multi-track sensor contains four capacitive sensors in one compact housing. This is how four tracks on the brake disc can be detected synchronously. Mirror-inverted sensor models mounted on the opposite sides of the brake disc enable accurate thickness measurement. A special ceramic substrate protects the sensors from mechanical and thermal loads, also providing high temperature stability, which enables precise measurement results in the case of fluctuating ambient temperatures.
|
|
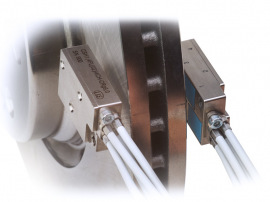 |
|
Combined with the DT6220 controller, four sensor channels can be configured and processed synchronously. Due to the high bandwidth, dynamic measurements up to 5kHz (-3dB) are possible. Data output is via an analog output or a digital Ethernet/EtherCAT interface. An intuitive web interface enables fast, easy set up and configuration of the sensor and controller. |
|
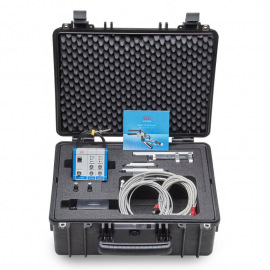 |
|
Case for mobile use
The case contains a 2-channel controller incl. software license, two capacitive sensors with corresponding cable and a bracket kit. The case enables thickness measurements of brake discs within a short period of time. The DTV data can be evaluated using a PC or notebook. The controller is activated for the Disc Thickness Variation Measurement Software from Micro-Epsilon. It is possible to hide the brake disc holes using special functions. Intelligent algorithms enable versatile evaluations without having to use an additional encoder.
|
|
|
|
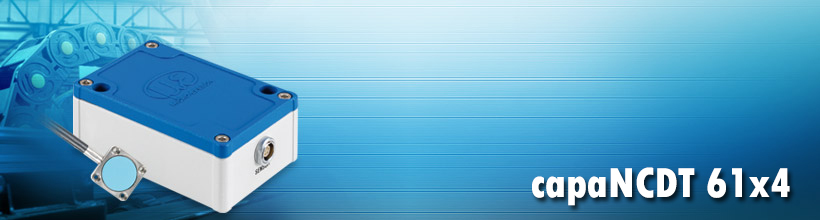 |
|
|
|
Inductive displacement sensors monitor the clamping position
|
|
|
|
 |
|
The capaNCDT DT61x4 is an active, capacitive system for displacement, distance and position measurements. Consisting of a sensor with integrated preamplifier, a robust cable and a compact controller, the measuring system is immediately ready for use without any on-site calibration. The measuring system is available with a cable length up to 15 m and is ideal for automation purposes. The capaNCDT 61x4 is particularly suitable for automated robot manufacturing and measurement tasks with a drag chain. Moreover, it is used in machine building and semiconductor production. For optimum signal quality, the desired cable length is already factory-calibrated. |
|
|
|
Compact and robust flat sensor
The active flat sensor is designed with a stainless steel housing and a ceramic sensor element. The cable integrated on the sensor side provides considerable advantages: it significantly reduces the required installation space while increasing the mechanical stability of the sensor.
|
|
Robust cables for robots and drag chains
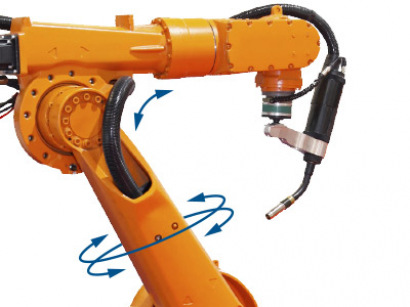 
Offering high flexibility and lengths up to 15 m, the robust capaNCDT 61x4 cables are ideally suited to measurement tasks on robots and in automation technology.
|
|
|
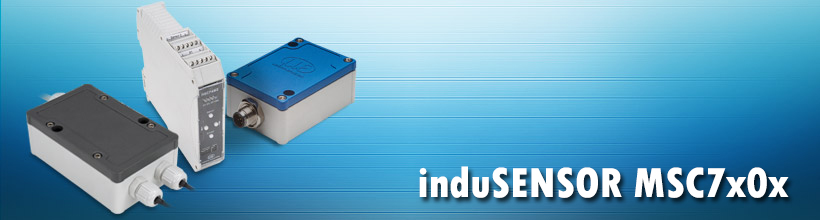 |
|
Universal controllers for inductive displacement sensors
|
|
The MSC controllers are designed to be operated with LVDT and LDR measuring gauges and displacement sensors. Due to the robust and compact aluminum housing, the controllers are ideal for industrial measurement tasks. A large variety of compatible, inductive displacement sensors and gauges combined with an optimized price/performance ratio opens up multiple fields of applications in automation technology and machine building. |
|
|
|
|
|
1-channel controller for inductive displacement sensors – induSENSOR MSC7401
|
|
|
New: 2-channel controller for inductive displacement sensors – induSENSOR MSC7802
|
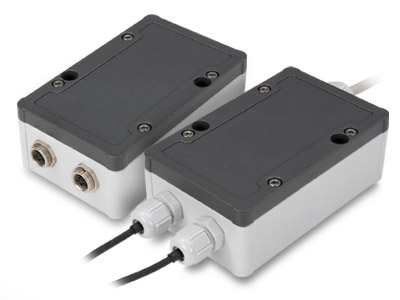
|
|
The MSC7802 controller is designed to be operated with LVDT and LDR measuring gauges and displacement sensors. Particularly for multi-channel applications, its optimized price/performance ratio opens up multiple fields of application in automation technology and in machine building. The controller has a bus connector which significantly reduces the wiring effort. Parameter setting is easily done via buttons or software.
|
|
|
New: 2-channel controller with DIN rail housing for inductive displacement sensors – induSENSOR MSC7602
|
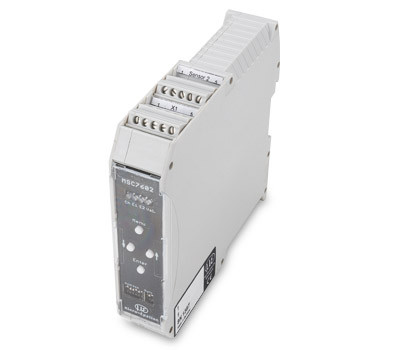
|
|
The MSC7602 controller is designed to be operated with DTA (LVDT) and LDR measuring gauges and displacement sensors. Its optimized price/performance ratio opens up multiple fields of application in automation technology and in machine building. This makes the controller ideally suitable for multi-channel applications. The bus connector on the rear side significantly reduces the wiring effort. The controller is easily set up using buttons/LEDs or software.
|
|
|
|
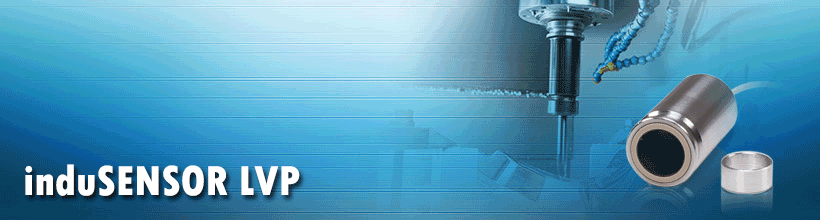 |
|
Inductive displacement sensors monitor the clamping position
|
|
The induSENSOR LVP offers a significant improvement to monitor the clamping position in machine tools. The sensor is integrated into the release device and directly measures the clamping stroke of the drawbar onto which the target ring is glued. Its extremely compact design allows for the sensor to be integrated into different tool types while providing high precision and continuous monitoring. No adjustment is necessary when changing the tool. |
|
|
|
|
|
|
|