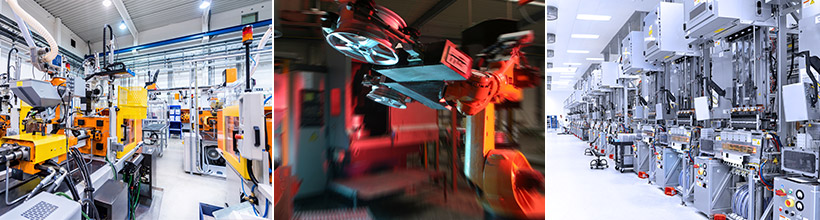 |
|
Automation
|
Increasing networking in factory and plant automation requires the immediate availability of all relevant operating information. Here, intelligent networking of development, production and logistics is a central challenge. Smart sensors from Micro-Epsilon ensure the optimal integration and networking of machines and processes due to their versatile industry interfaces and evaluation algorithms. Thanks to their high precision, the sensors often replace switches in order to react to events more quickly and accurately. |
|
Position detection of car bodies in the processing line
|
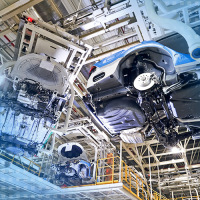 |
Before a car emerges from a bodyshell, it passes through numerous stations within the production, in which fully automatic processing steps are carried out. In order to enables the processing robots to recognize the exact position of the car body, several laser triangulation sensors measure the car body and transmit the position data to the robot controller.
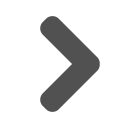 Smart laser triangulation displacement sensor
|
|
|
Measuring applied adhesive of tapes, plasters and Band-Aids
|
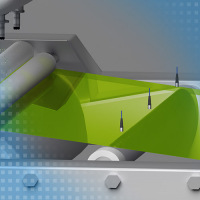 |
To ensure a homogeneous adhesive surface, capacitive displacement sensors measure the thickness of the adhesive on adhesive tapes and medical plasters. Capacitive sensors allow one-sided thickness measurement. Depending on the system structure, conductive or non-conductive adhesives can be measured.
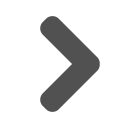 Capacitive displacement sensors and measurement systems
|
|
|
High precision thickness measurement of silicon wafers
|
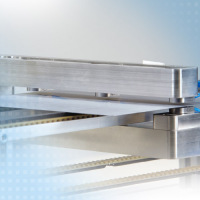 |
Capacitive displacement sensors are used for the exact thickness measurement of wafers. Two opposing sensors detect the thickness and also determine other parameters such as deflection or sawing marks. The position of the wafer in the measuring gap may vary.
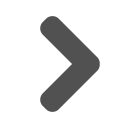 Capacitive displacement sensors and measurement systems
|
|
|
Presence detection of small parts
|
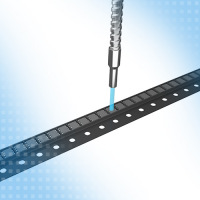 |
In assembly processes, incoming components are inspected using Micro-Epsilon fiber optic sensors. Recognizing missing SMT components enables a smooth assembly process. Their flexible design allows for the optoCONTROL CLSK probe heads to be integrated in confined spaces.
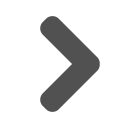 Fiber optic sensors for gap, diameter, edge and presence
|
|
|
Thickness measurement of black rubber belts
|
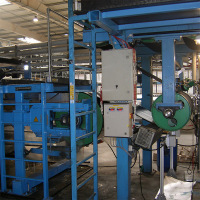 |
Rubber mats for the structure sealing must exhibit a specified thickness for durability and tear resistance. The thickness of the films is measured directly after the extrusion. The optoNCDT 1750 sensors used measure the distance to the rubber despite poor reflectivity. The thickness is determined from the sensor signal and the distance to a reference roller. The user thus recognizes already starting deviations from the target thickness.
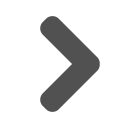 Universal laser sensor for industry & automation
|
|
|
Orientation of wooden boards
|
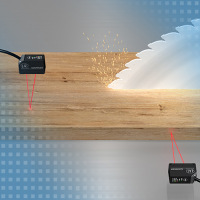 |
In fully automated sawmills, the position of wooden boards before sawing must be determined so that they can be cut precisely. Micro-Epsilon laser displacement sensors detect the position of the boards from two sides and output the board position to the controller.
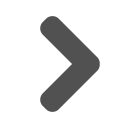 Smart laser triangulation displacement sensor
|
|
|
Inspection of plate position
|
 |
When printing woods with decors, optoCONTROL micrometers are used to control the positions of the plate. This prevents the printing head from colliding with the plate. These laser micrometers measure directly on wood and monitor the tools.
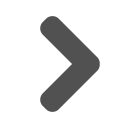 High resolution optical micrometer
|
|
|
Inspection of wood floorboard relief
|
|
|
Profile inspection of parquet flooring and baseboards
|
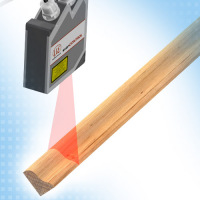 |
Laser scanners from Micro-Epsilon are used for the profile measurement of parquet boards and baseboards. They inspect geometric characteristics such as groove height, gap dimensions and absolute dimensions to ensure homogeneous product quality.
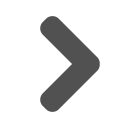 Laser scanners for 2D/3D profile measurements
|
|
|
Color recognition of kitchen fronts
|
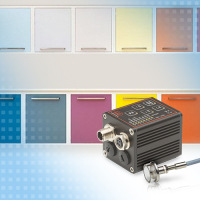 |
In order to ensure consistent color of different front panels, color sensors from Micro-Epsilon are used. The sensors inspect the color of the kitchen fronts in the painting plant. Color sensors ensure that the color shade is within the specified tolerances. Even the smallest color deviations imperceptible to the human eye can be detected reliably.
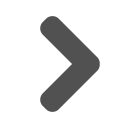 Compact True Color Sensor
|
|
|
Dimension control of beams
|
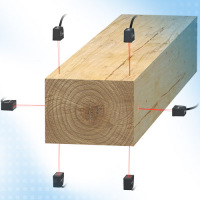 |
For thickness and width measurement of plates, planks and beams, two optoNCDT laser sensors are used. If this arrangement is complemented by further sensors, one synchronized measurement process can combine the inspection of torsion with control of dimensions.
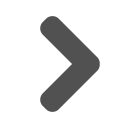 Smart laser triangulation displacement sensor
|
|
|
Color inspection and sorting of supplier parts
|
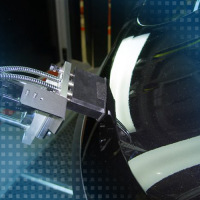 |
Before installing front aprons, Micro-Epsilon color sensors check if the color of the attachment matches the body color. Different color groups can be defined to cover all coatings.
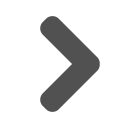 Compact True Color Sensor
|
|
|
Color measurement of the floorboards
|
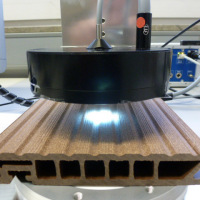 |
Plastic floorboards are made of colored granules and shaped by deep-drawing. After the production process, it must be guaranteed that the color of the floorboards is homogenous and that there are no color differences.
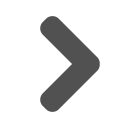 High Speed Photospectrometer colorCONTROL ACS7000
|
|
|
In-line detection of protective film on PVC window frames
|
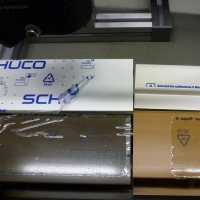 |
Company „Schüco“ manufactures PVC window frames. The PVC profiles are provided with a protective film after they are extruded. This film protects the frames from scratches and dirt. The colorCONTROL ACS7000 color measurement system checks if the protective film has been applied correctly.
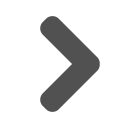 High Speed Photospectrometer colorCONTROL ACS7000
|
|
|
Calibrating robot axes
|
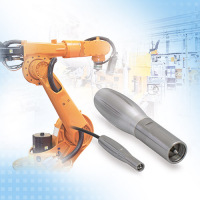 |
Industrial robots have become indispensable in modern production facilities due to their reliability and high speed. During set up and also at regular intervals within the scope of quality assurance, the robot axes must be adjusted. Here, electronic adjustment probes have already replaced mechanical probes. The measurement probes mounted on the robot axes acquire the zero point during the axis rotation using a probe tip. The integral electronics evaluates the probe signal and transmits a switching signal to the robot controller.
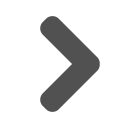 induSENSOR LVDT gages DTA series
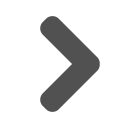 Inductive sensors (LVDT) and gauges
|
|
|
|