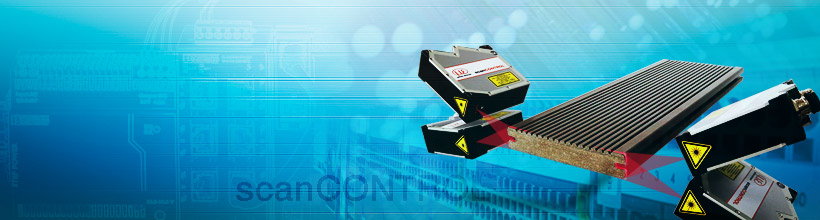 |
|
Measurement value evaluation
|
|
Comprehensive, flexible evaluation of measured values from several sensors using scanCONTROL Smart PLC Unit. |
|
|
|
|
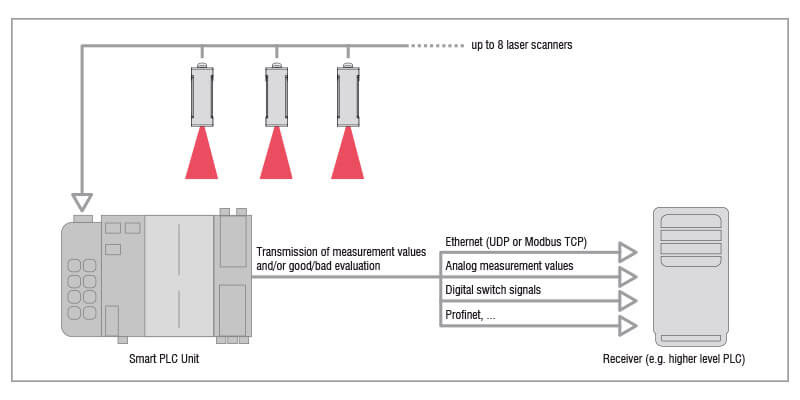 |
|
|
|
White light interferometer for absolute distance measurement with subnanometer accuracy Product Technology
|
|
|
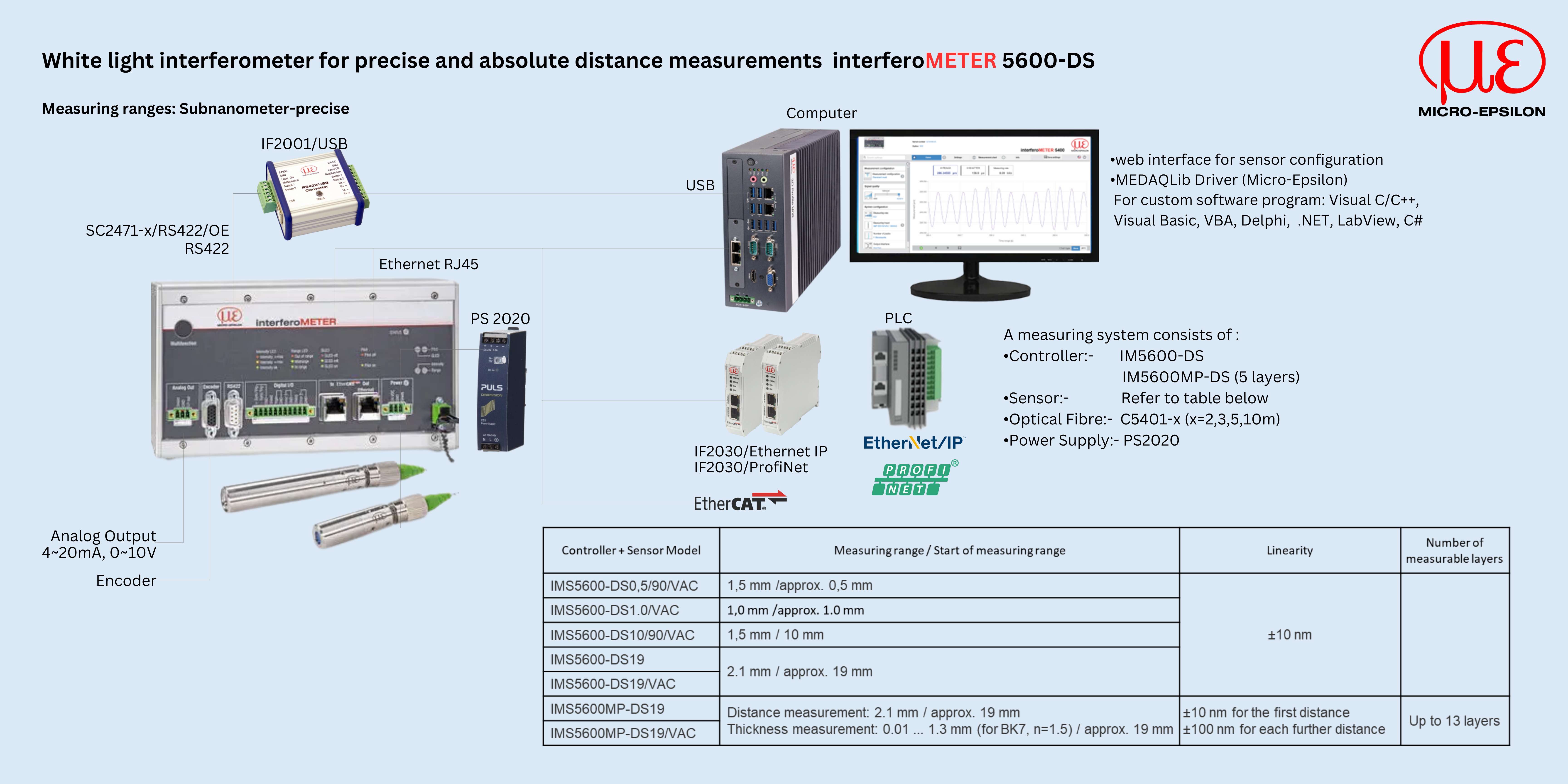 |
|
The new white light interferometer IMS5600-DS is used for distance measurements with highest precision. The controller offers a special calibration with intelligent evaluation and enables absolute measurements with subnanometer resolution. The interferometer is used for measurement tasks with the highest accuracy requirements, e.g., in electronics and semiconductor production. |
|
|
|
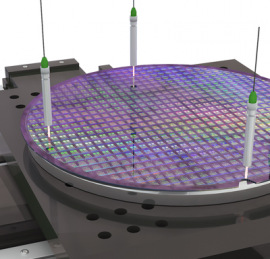 |
|
Absolute distance measurement with large measuring range and offset distance
The IMS5600-DS is used for high-precision displacement and distance measurements. The system provides absolute measurement values and can therefore also be used for distance measurement of step profiles. Thanks to the absolute measurement, steps are sampled with high signal stability. When measuring on moving objects, the differences in height of heels, steps and depressions can thus be reliably detected. The measuring system offers sub-nanometer resolution with a large offset distance in relation to the measuring range.
|
Designed for high-resolution distance measurements in vacuum
IMS5600-DS interferometers can be used for measurement tasks in vacuum environments and clean rooms where the interferometers achieve a resolution in the subnanometer range. For vacuum applications, Micro-Epsilon offers special sensors, cables and feed-through accessories. These sensors and cables are particle-free to a high degree and can be used from clean rooms to UHV.
|
|
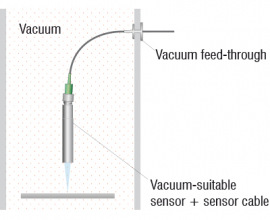 |
|
Stable distance measurements with highest precision
The controller can be installed in the control cabinet via DIN rail mounting and provides very stable measurement results thanks to active temperature compensation and passive cooling. These compact sensors are extremely space-saving and have highly flexible fiber optic cables. Cable lengths up to 10 m allow a spatial separation of sensor and controller. The sensor can be aligned easily and quickly due to the integrated pilot laser. Commissioning and parameterization are conveniently performed via web interface and do not require any software installation.
|
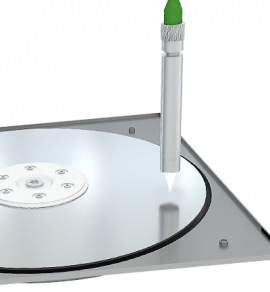 |
|
Measurement on multiple surfaces
The interferometric measuring method allows measurements on numerous surfaces. This enables high-precision distance measurements on reflecting metals, plastics and glass.
|
|
|
|
|
|
White light interferometer for stable thickness measurement with submicron accuracy Product Technology
|
|
|
|
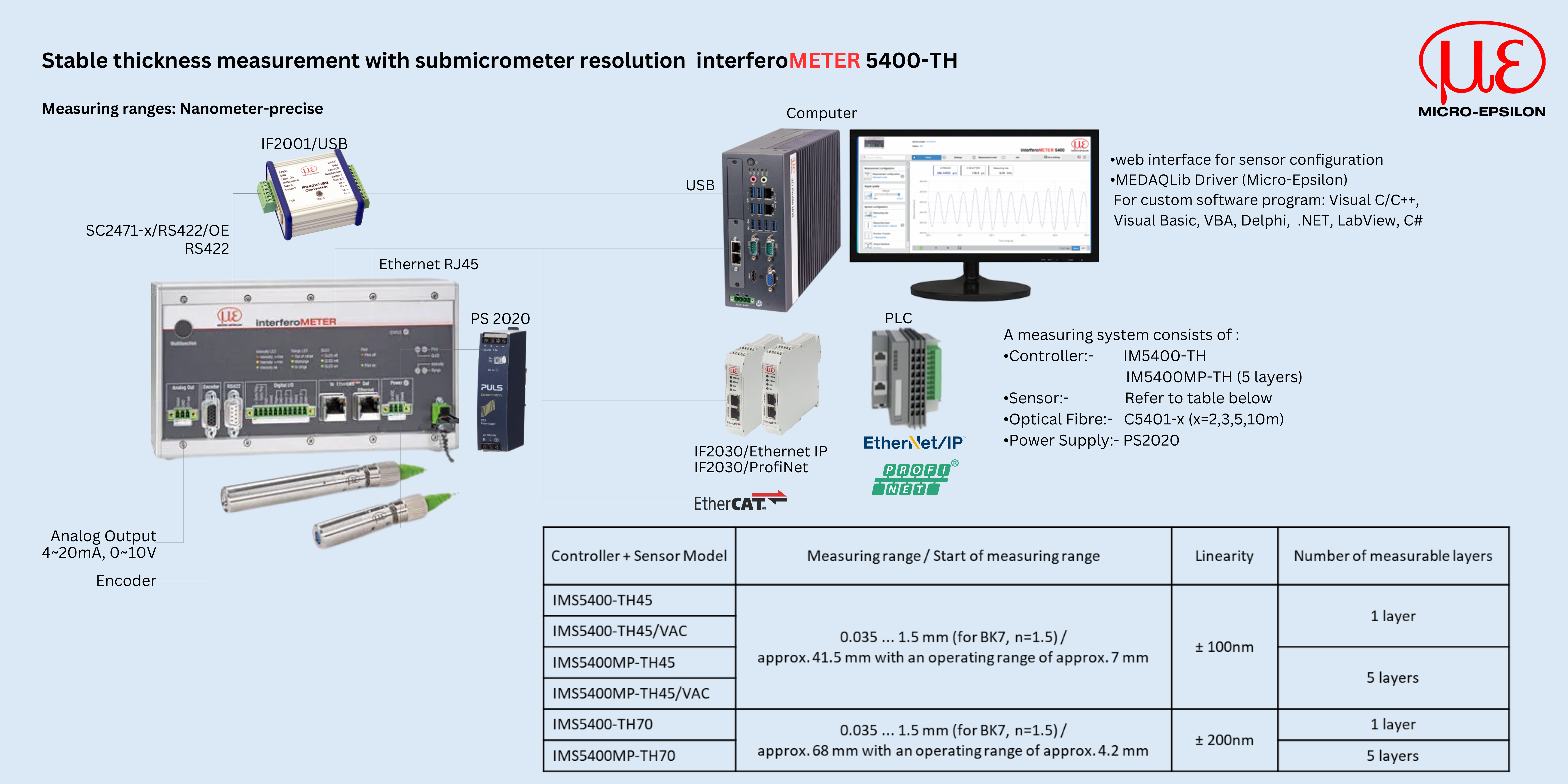 |
|
|
The new IMS5400-TH white light interferometer opens up new perspectives in industrial thickness measurement. The controller offers an intelligent evaluation feature and enables the thickness measurement of transparent objects with highest precision. |
|
|
|
The IMS5400-TH white light interferometer is used for highly accurate thickness measurements from a relatively large distance. A decisive advantage here is the distance-independent measurement, where a nanometer-accurate thickness value is achieved even with moving objects. The large thickness measuring range allows the measurement of thin layers, flat glass and films. Since the white light interferometer works with an SLED in the near infrared range, thickness measurement of anti-reflective coated glass is also possible.
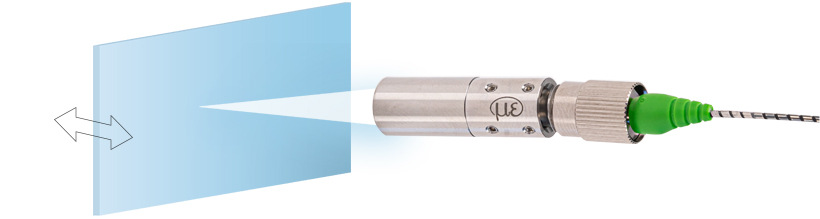
Thickness measuring ranges Air gap measurement (with refractive index ~1) 50 µm to 2.1 mm Glass thickness measurement (with refractive index ~1.5) 35 µm to 1.4 mm
|
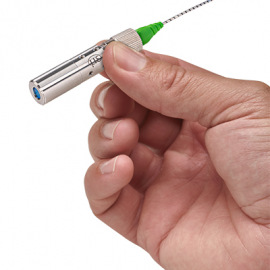
|
|
Ideal for industrial environments
Robust sensors and a controller in a metal housing make the system ideally suitable for integration into production lines. The controller can be installed in the control cabinet via DIN rail mounting and provides very stable measurement results due to active temperature compensation and passive cooling. These compact sensors are extremely space-saving and have highly flexible fiber optic cables. Cable lengths up to 10 m allow a spatial separation of sensor and controller. The sensor can be aligned easily and quickly using the integrated pilot laser. Commissioning and parameterization are conveniently performed via web interface and do not require any software installation.
|
|
|
|
|