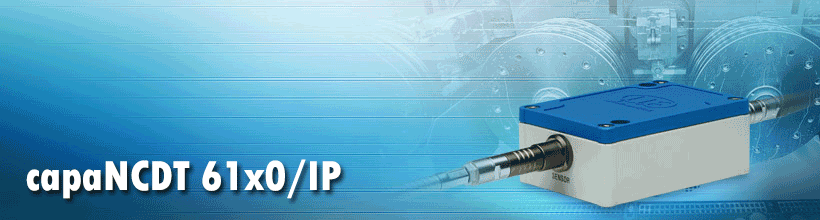 |
|
|
|
Industrial-grade, capacitive controller with voltage output – DT6110/IP controller
|
|
Protected to IP68, the DT6110/IP capacitive controller is designed for measurement tasks in industrial environments. The DT6110/IP controller is available with either a voltage or current output, and can also be used in confined spaces due to its compact design. |
|
Industrial-grade, capacitive controller with RS485 interface – DT6120/IP controller
|
|
Classified to IP68, the DT6120/IP capacitive controller is designed for measurement tasks in industrial applications. In addition to either a voltage or current output, the DT6120/IP controller offers an RS485 interface. Due to its compact design, the controller can also be used in confined spaces. |
|
|
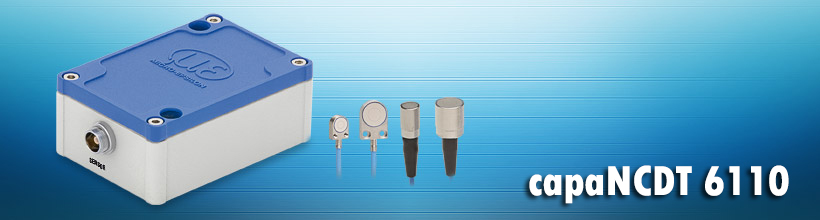 |
|
|
|
Compact capacitive controller with high resolution – DT6110 controller
|
|
The capacitive DT6110 controller is the entry model for high resolution, capacitive displacement measurement. Due to its extremely compact size, the controller can also be integrated into restricted installation spaces. The DT6110 controller is compatible with all sensors and cables of the capaNCDT series. The DT6110/ECL2 controller provides an extended cable length. |
|
Capacitive controller for dynamic measurement tasks up to 20kHz (-3dB) – DT6112 controller
|
|
The capacitive DT6112 controller is the entry model for dynamic measurement tasks. A bandwidth of up to 20kHz (-3dB) enables reliable monitoring of fast processes. The DT6112 controller is compatible with all sensors and cables of the capaNCDT series. |
|
Compact capacitive controller with RS485 interface – DT6120 controller
|
|
Equipped with an analog output and an RS485 interface, the capacitive DT6120 controller is the entry model for high resolution, capacitive displacement measurement. Due to its extremely compact size, the controller can also be integrated into restricted installation spaces. The DT6120 controller is compatible with all sensors and cables of the capaNCDT series. |
|
|
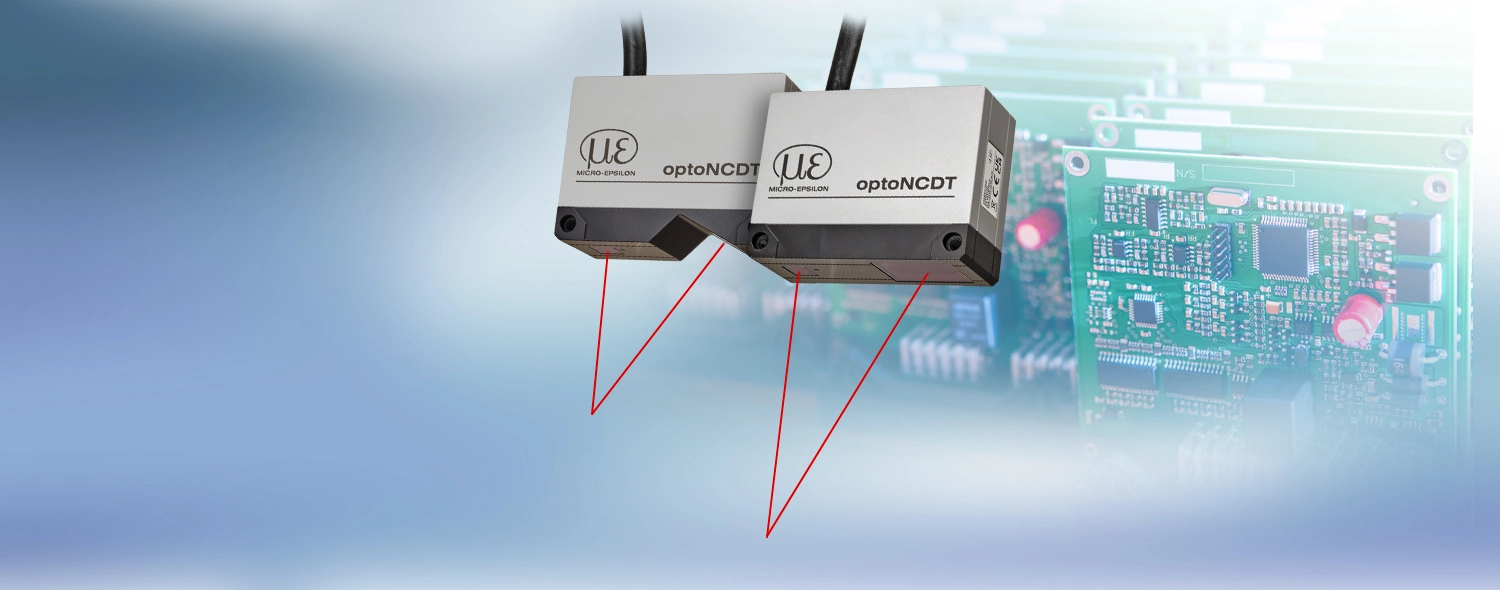 |
|
Highly dynamic laser sensor up to 75 kHz
|
|
|
|
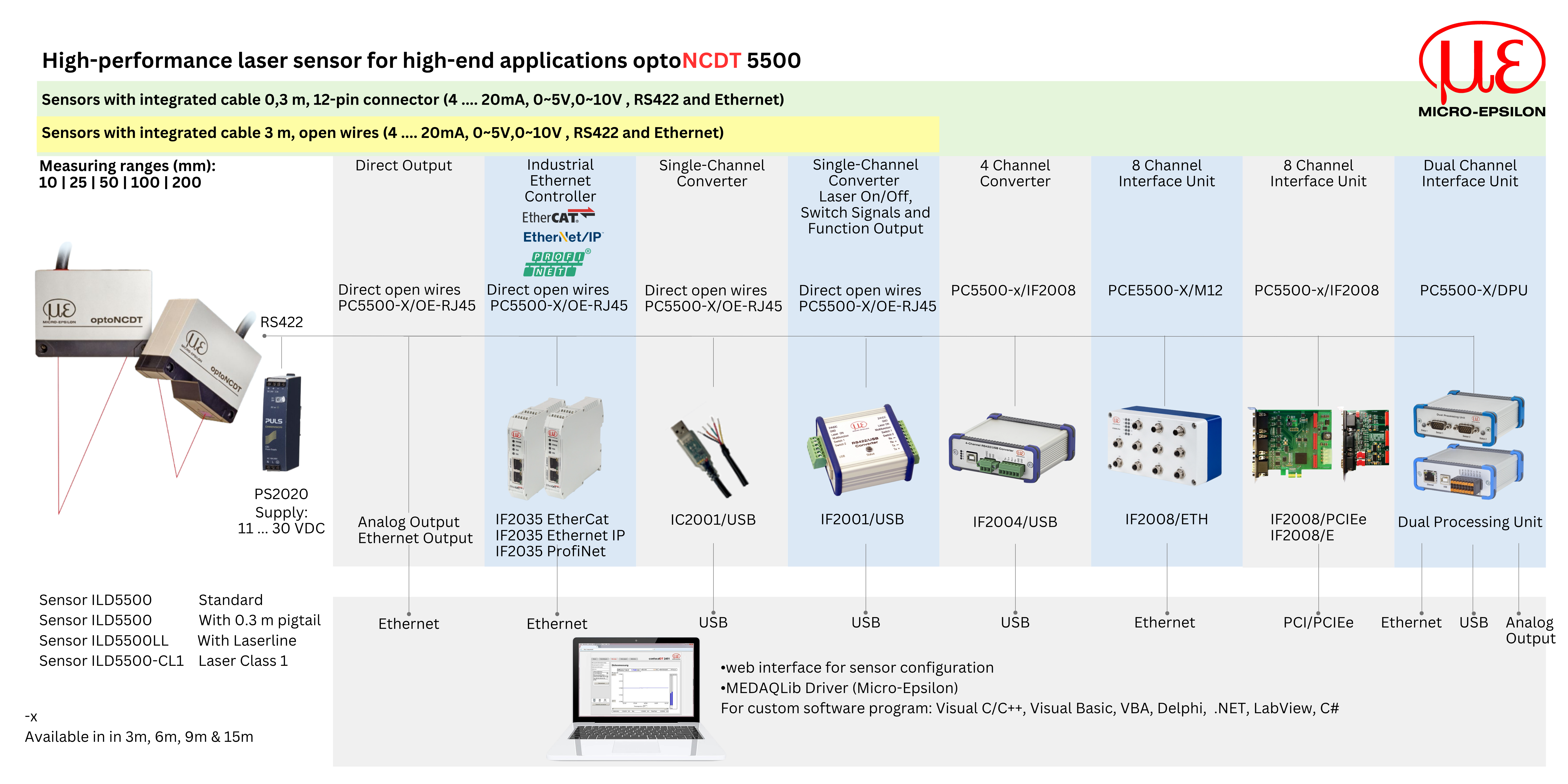 |
|
The optoNCDT 5500 laser sensors set new standards in high-precision laser distance measurement. With submicron precision and an impressive measuring rate up to 75 kHz, the sensors are perfect for dynamic measurements of displacement, distance, vibration and position. Due to its integrated controller, the compact sensor does not require any external control units and can be easily integrated even in confined installation spaces. Maximum performance in the smallest of spaces - the optoNCDT 5500 series. |
|
|
|
Versatile use
|
|
The optoNCDT 5500 sensors are available with different measuring ranges. In addition to the standard measuring range, an extended measuring range can be used, which significantly expands the fields of use. With IP67 protection and high resistance to ambient light, the laser sensor can also be used in challenging environmental conditions. |
|
Highest performance: A new class of laser triangulation sensors
|
|
The optoNCDT 5500 from Micro-Epsilon represents the latest performance class among laser triangulation sensors. With its increased measuring rate of up to 75 kHz, the sensor is ideal for highly dynamic measurement tasks. This laser sensor delivers extremely precise measurement results, even on rapidly changing and poorly reflective surfaces. Its high repeatability enables measurements with submicron precision.
|
|
 |
|
|
Advanced Surface Compensation - The intelligent exposure control for all surfaces
|
|
The optoNCDT 5500 is equipped with an intelligent surface control feature. New algorithms enable fast exposure control and therefore stable measurement results on surfaces where changing reflections occur. In addition, the sensor is extremely resistant to ambient light and can also be used in strongly illuminated environments. The new algorithms compensate for ambient light up to 50,000 lux.
|
|
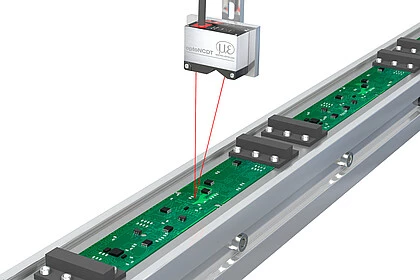 |
|
|
Simple mounting and initial operation
|
|
It is not necessary to align the sensor due to patented, repeatable mounting using mounting sleeves. This enables both easy sensor replacement and even higher precision in solving measurement tasks. Due to its small dimensions and the integrated controller, the laser sensor can also be installed in confined spaces. A web interface with ready-made presets makes the sensor immediately ready for use. The ILD5500 is more compact than its predecessor ILD2300. To enable a seamless changeover, Micro-Epsilon offers an adapter plate for a quick switch from ILD2300 to ILD5500.
|
|
 |
|
|
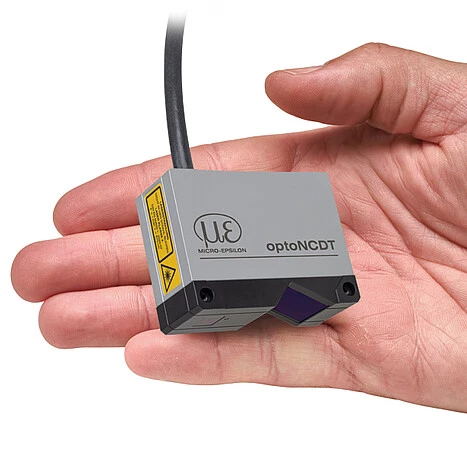 |
|
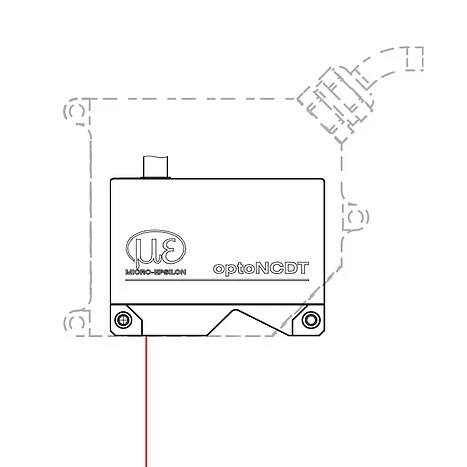 |
|
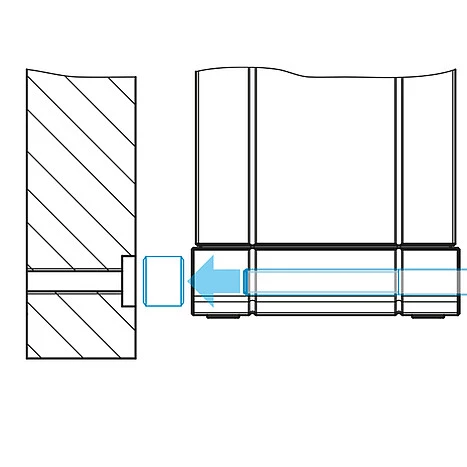 |
|
|
|
|
|
Space-saving design, no external controller required |
|
Adapter plates for replacing optoNCDT 2300 sensors |
|
Patented mounting concept for repeatable fastening |
|
|
Applications
|
|
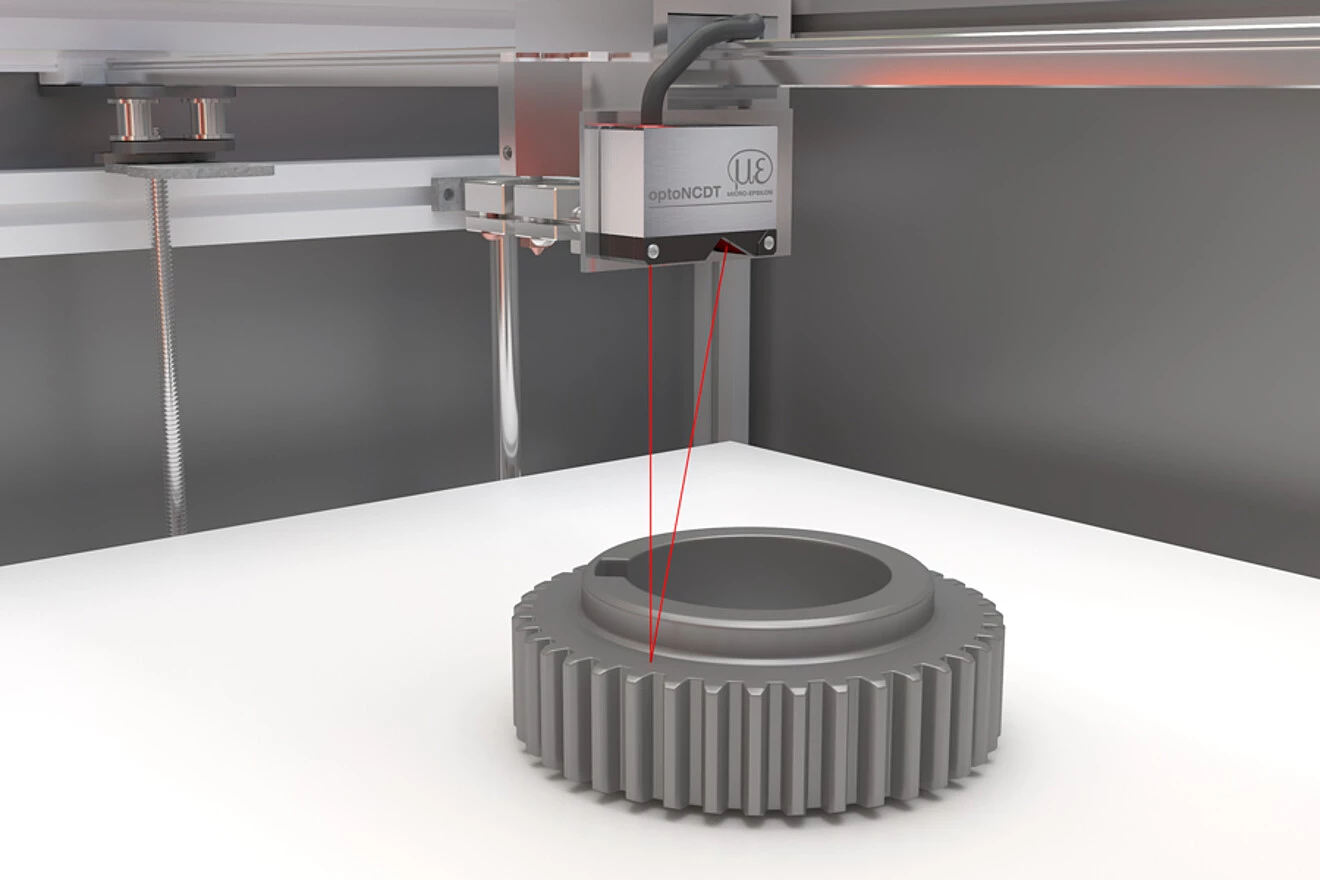 |
|
 |
|
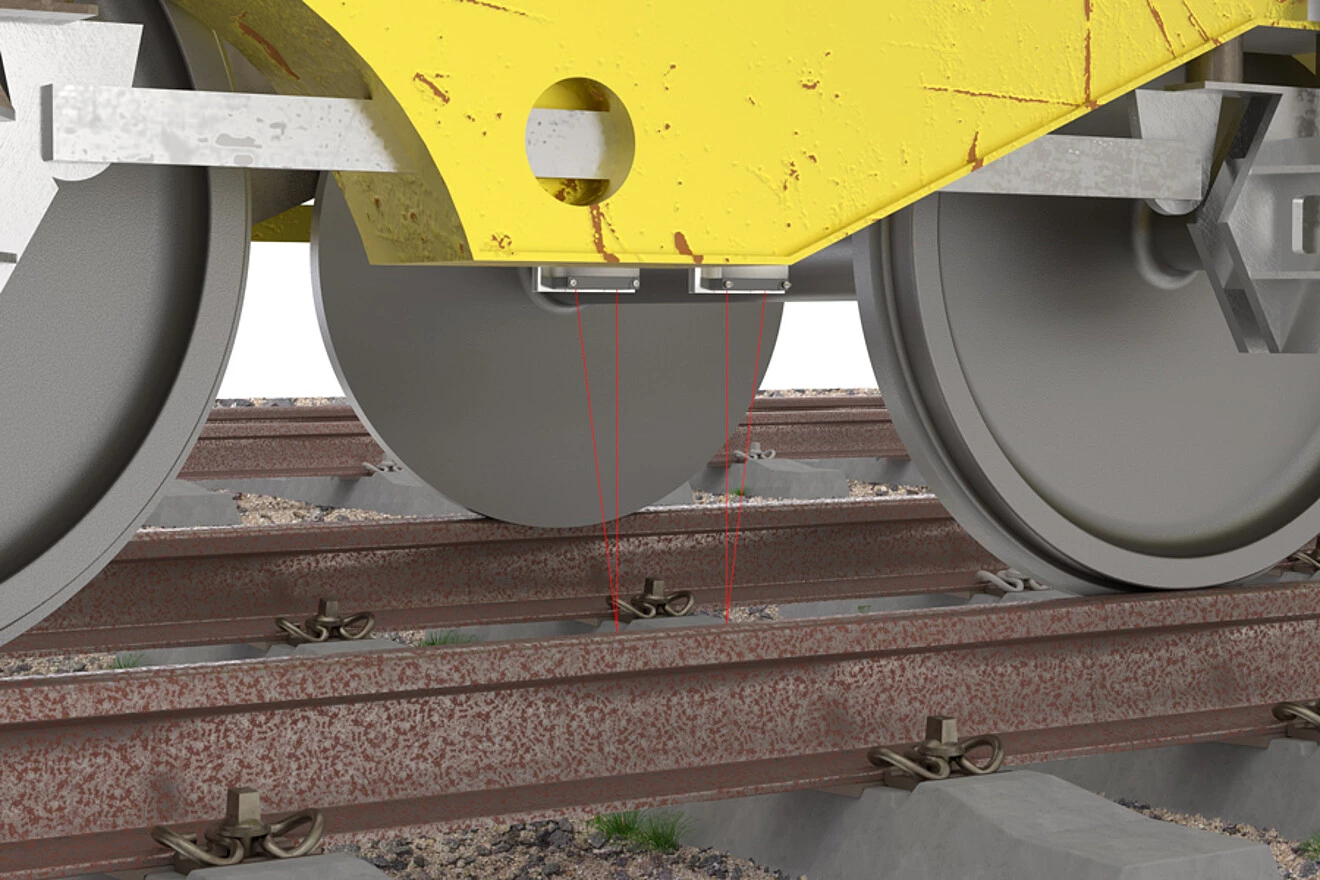 |
|
|
|
|
|
Positioning the print head in additive manufacturing |
|
Distance monitoring on black rubber |
|
Wear test on rails |
|
|
|
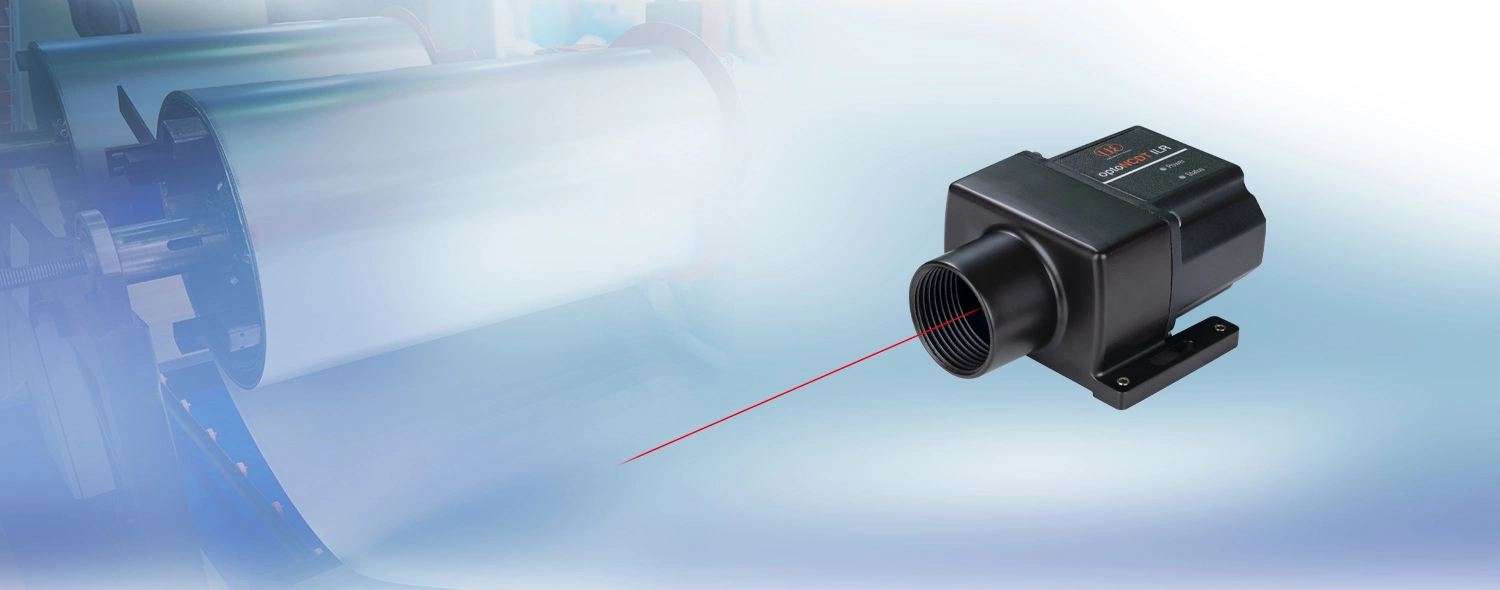 |
|
Powerful laser distance sensor
|
|
|
|
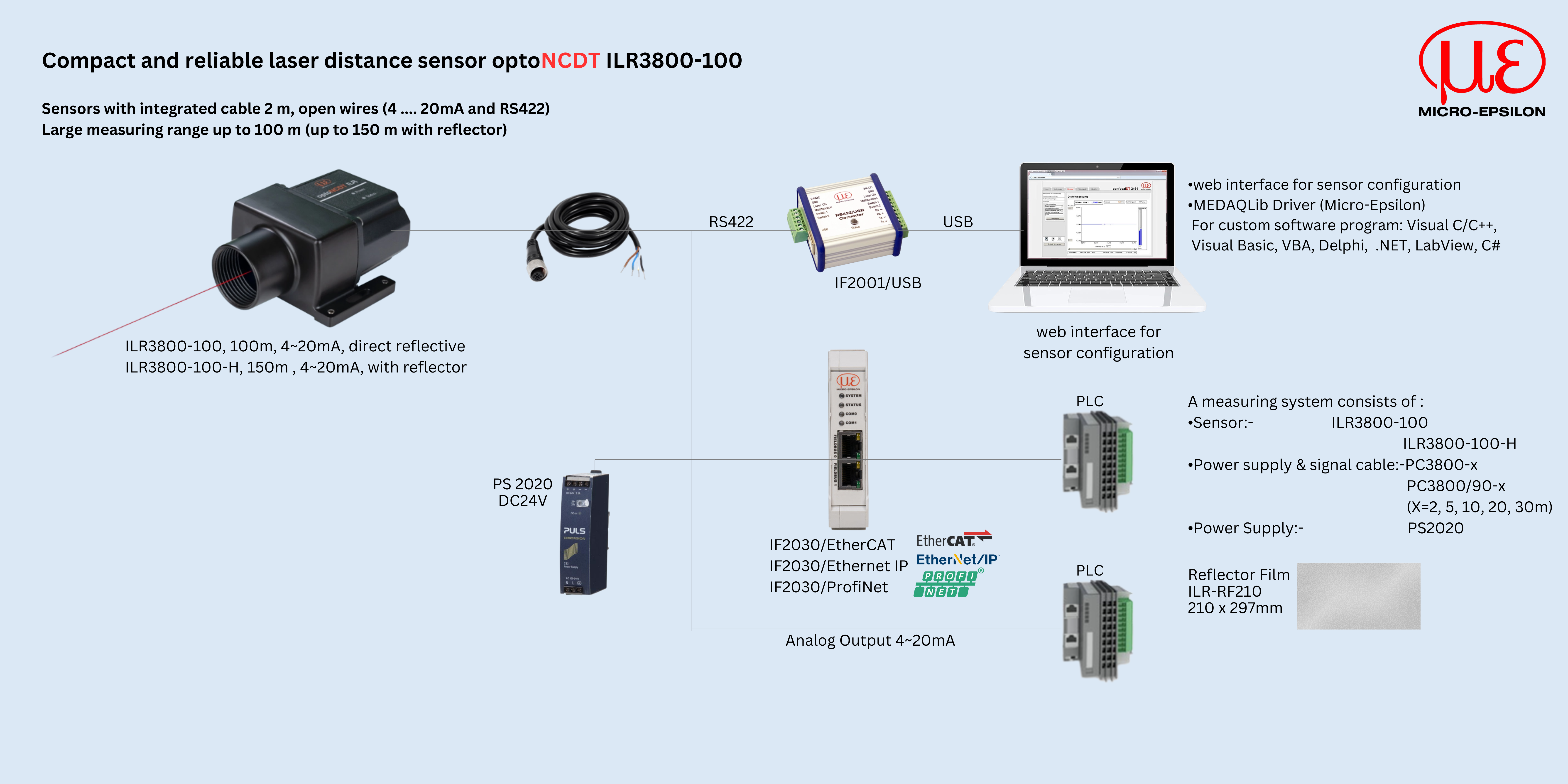 |
|
The optoNCDT ILR3800-100 laser distance sensor stands out in particular due to its high performance in a compact design. It is designed for precise distance measurements in industrial environments. Distance measurements up to 100 m are possible. With reflector even up to 150 m. The integrated AUTO measurement mode enables reliable measurement even on dark, partly reflecting and remote measuring objects. Thanks to the very high signal stability, ILR3800-100 sensors can be used for distance measurements on numerous surfaces. |
|
|
|
Compact sensor design for versatile measurement tasks
|
|
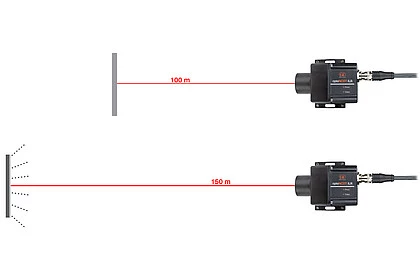 |
|
The laser distance sensor impresses with very high signal stability and is, among other things, used in logistics and automation technology, the metals industry and production monitoring. The robust aluminum housing and low weight allow easy integration into numerous industrial environments. |
|
|
|
The ILR3800-100 detects distances up to 100 m (without reflector), with reflector up to 150 m. This means the sensor is suitable for measurements tasks in logistics, factory and plant automation, as well as in drone applications for distance measurements from the air. |
|
New ILR3800-100-H with integrated heating for outdoor use
|
|
The ILR3800-100-H model has an integrated heating and cooling element that enables operation in the temperature range of -40 to +55 °C. This makes the sensor perfectly suitable for permanent outdoor use.
|
|
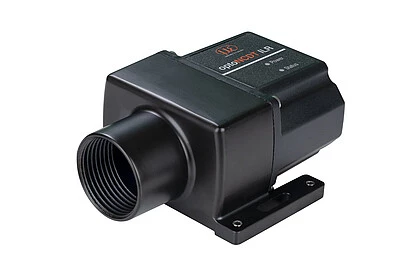 |
|
|
Mounting plate as optional accessory
|
|
You can easily replace the previous ILR2250-100 model with the new ILR3800-100 laser distance sensor. The mounting plate makes the changeover quick and easy.
|
|
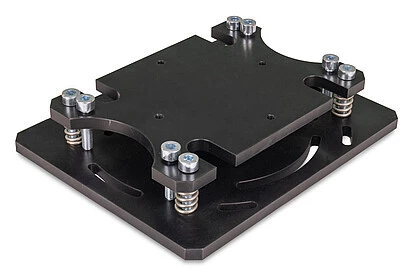 |
|
|
Workpiece positioning in CNC machining
|
|
Due to its robust and compact design, the powerful optoNCDT ILR3800-100 laser distance sensor is ideal for monitoring the position of large measuring objects such as rails. Over a total length of up to 3 m, the entire workpiece is detected by ten laser sensors. Due to the high accuracy and signal stability of the sensor, exact positioning on the clamping system of the CNC machine tool is possible. This ensures precise processing of the rails and reduces the error rate to a minimum.
|
|
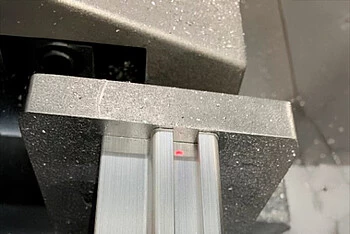 |
|
|
|
|
|
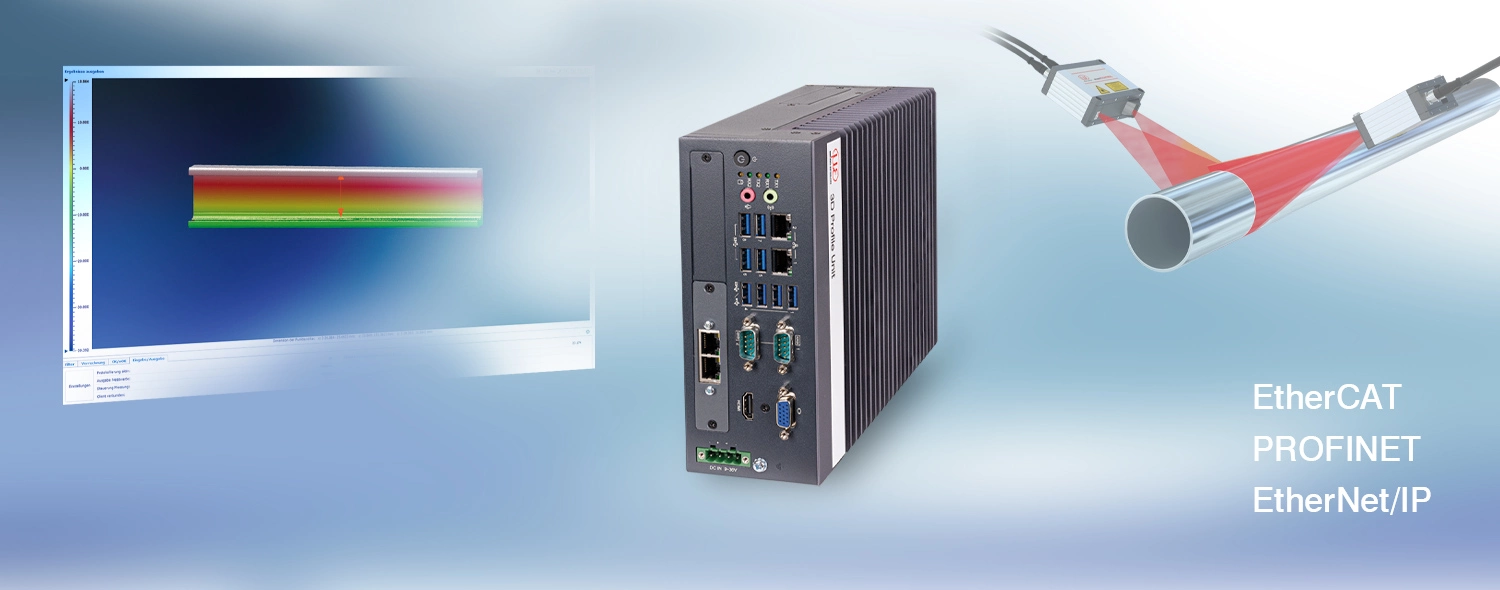 |
|
3D Profile Unit – Smart 3D evaluation and results output of stitched 2D/3D profile data
|
|
The 3D Profile Unit enables the calculation of several individual profiles of scanCONTROL 30xx sensors in a common coordinate system. This is how a composite 2D profile or a composite 3D point cloud can be generated. So the detection of various geometries, the extension of measuring ranges and the performance of thickness measurements is possible. The exact assignment of the position of the sensor to the position of the measurement object can be carried out via the integrated encoder inputs.
The evaluation of the data and the parameterization of the system can be implemented in the 3DInspect software. The 3D Profile Unit controller has an integrated evaluation feature in conjunction with the Industrial Ethernet connection, enabling the application to be controlled and measured values to be output to a PLC. Alternatively, the 3D Profile Unit controller can also be integrated into common image processing programs via GigE Vision and acts as a raw data provider.
|
|
|
|
|
|
3DInspect: Powerful software for all Micro-Epsilon 3D sensors
|
|
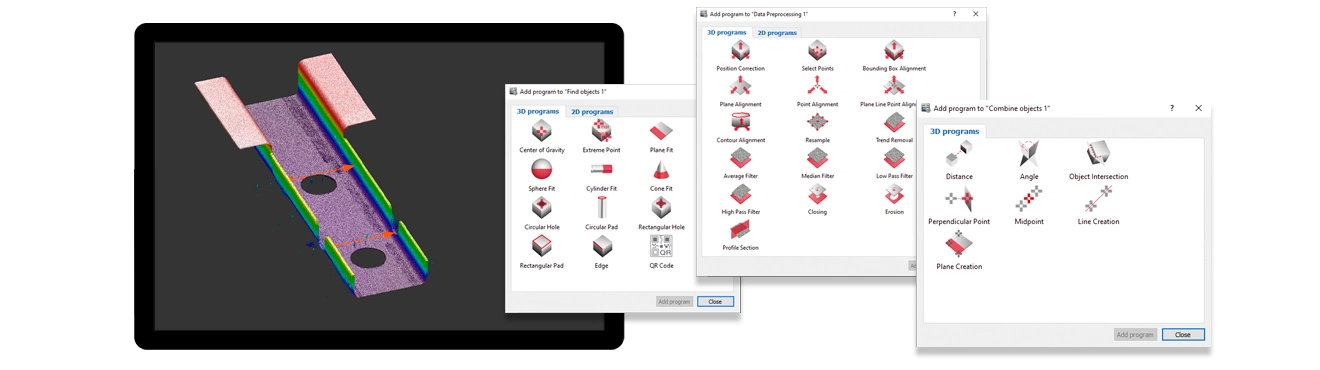 |
|
3DInspect is a standardized and user-friendly software tool for the 3D Profile Unit. This software can directly parameterize the 3D Profile Unit and record the measured data. Powerful tools allow point cloud alignment and filtering, intuitive detection and selection of relevant areas, and program combination. The 3D point clouds can be processed as required and measured values can be output to the controller. |
|
Generation and transfer of stitched 2D/3D profile data: 3DPU-X
|
|
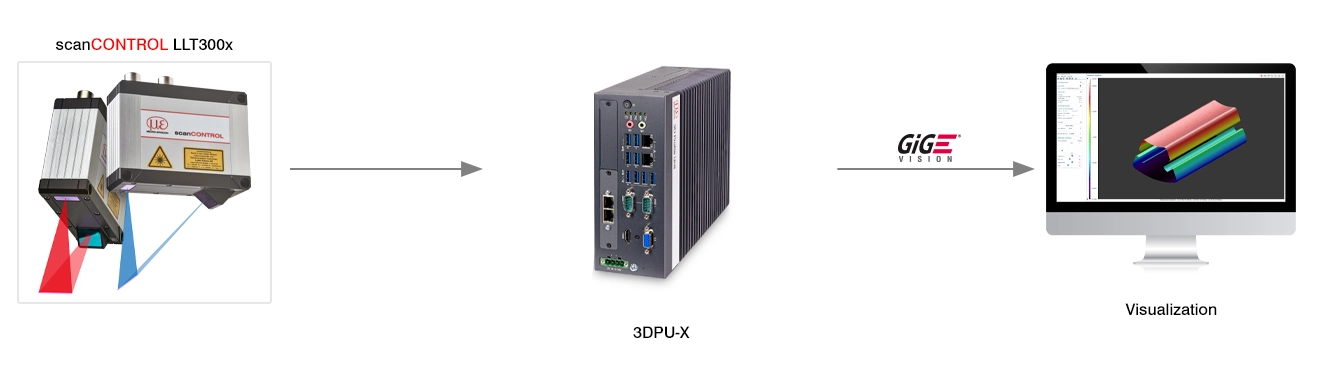 |
|
3DPU-X is a system that converts the profile data of several scanCONTROL sensors into a common coordinate system and makes it available as 2D profiles / 3D point clouds via GigE Vision.
Direct integration into image processing and 3D software | Communication with any GigE Vision clients | Transfer of profile data or 3D point clouds
|
|
Smart 3D evaluation and result output of stitched 2D/3D profile data: 3DPU-X/IE
|
|
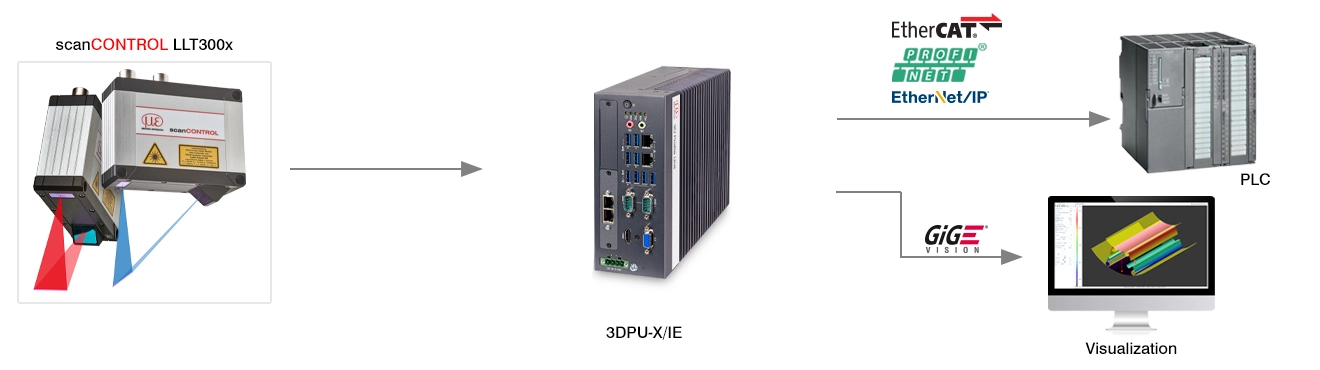 |
|
3DPU-X/IE is a system that converts the profile data of several scanCONTROL sensors into a common coordinate system, evaluates the 2D profiles / 3D point clouds and makes the measured values available via integrated fieldbus interfaces, e.g. as good or bad results.
Integrated evaluation and configuration via 3DInspect | Industrial Ethernet interface for control and transfer of measured values | Transfer of measured values and measurement results
|
|
Micro-Epsilon registration targets for automatic registration
|
|
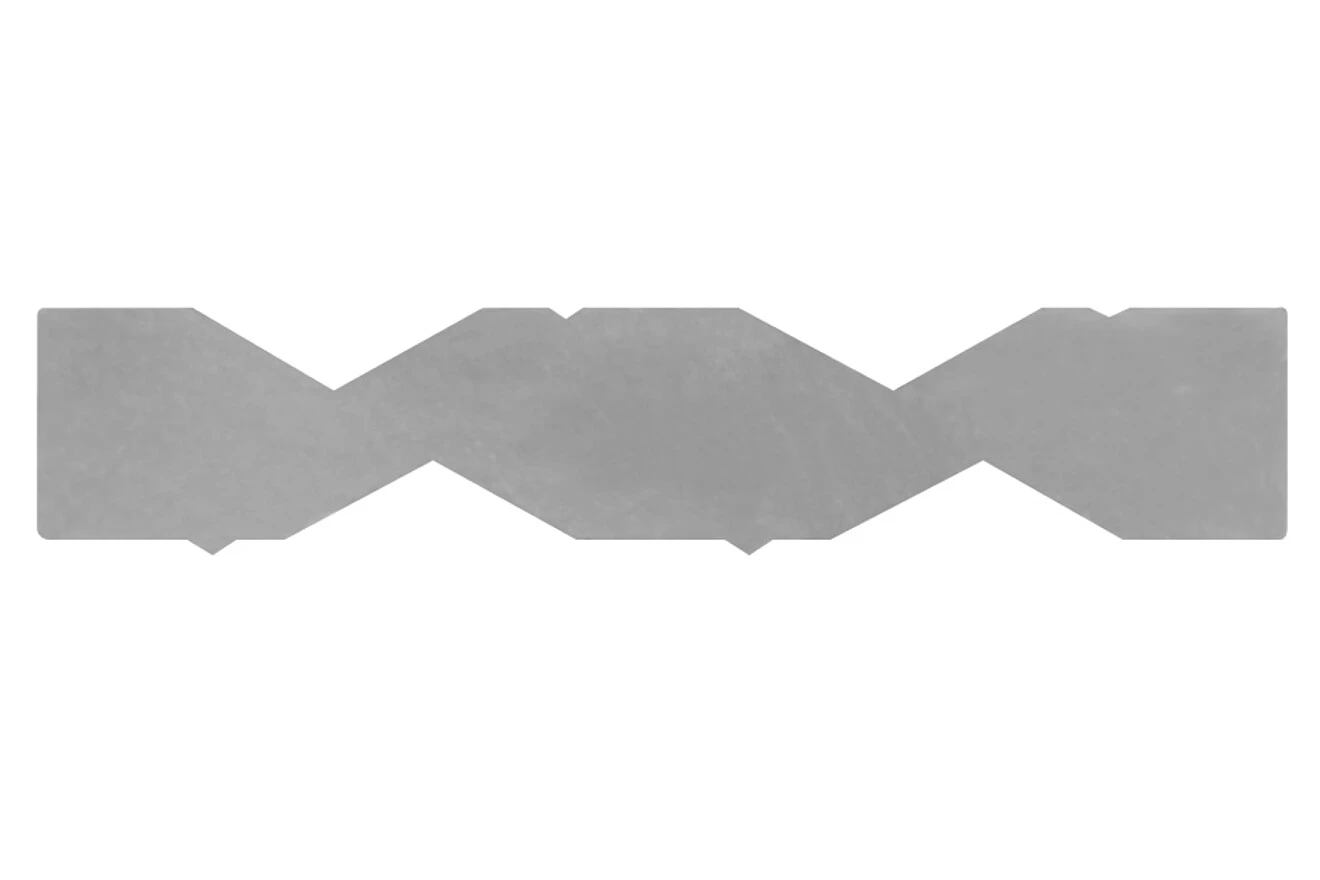 |
|
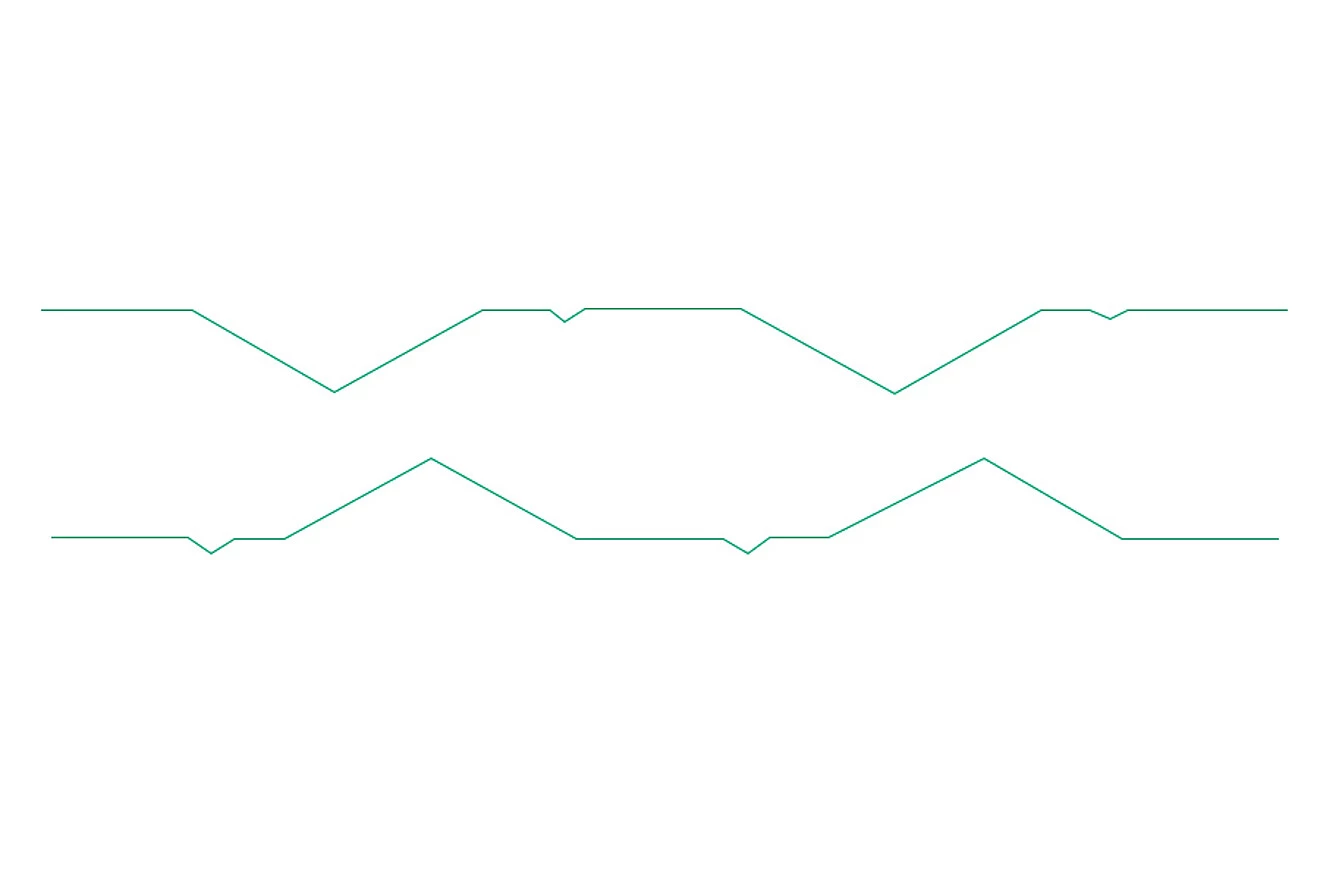 |
|
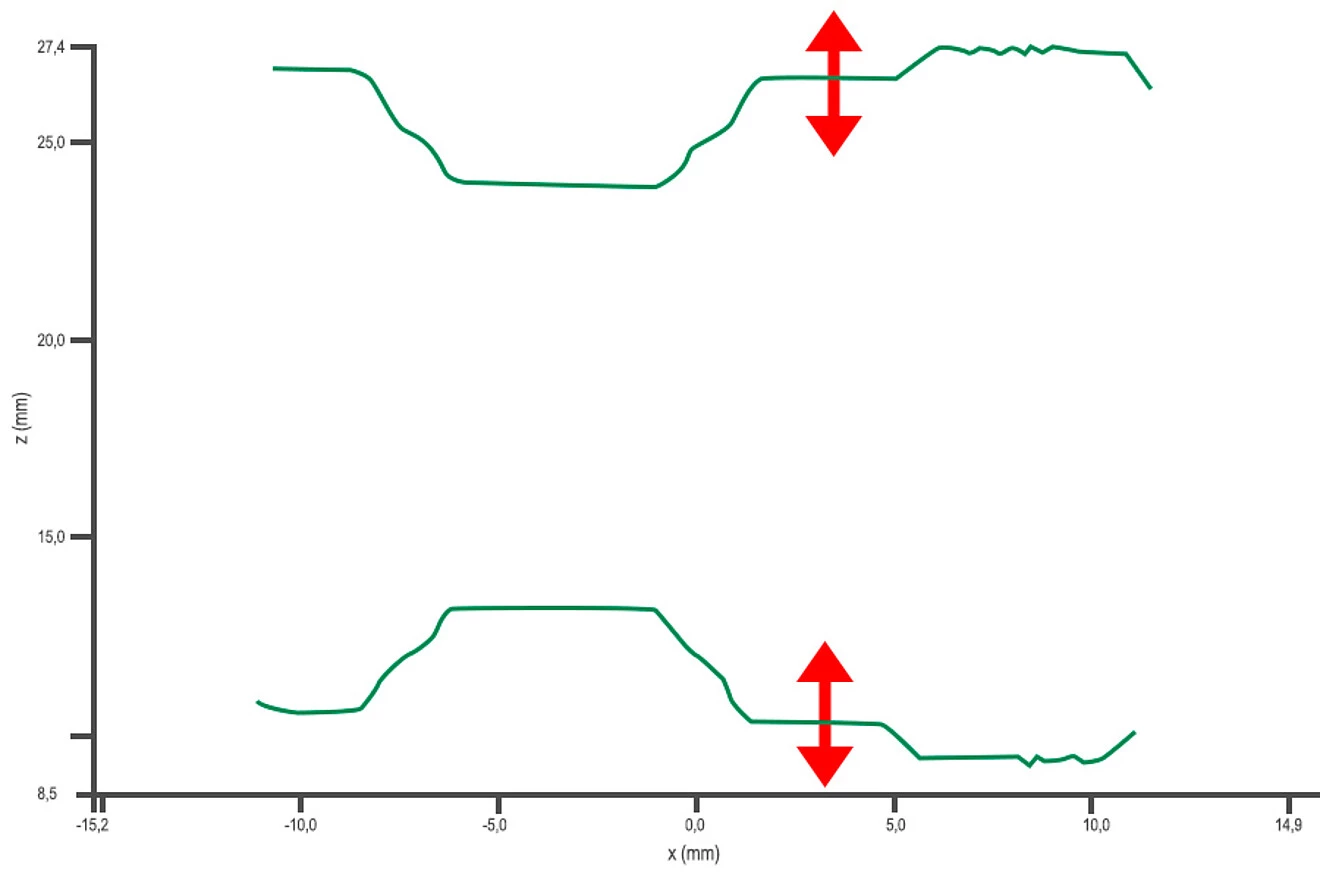 |
Automatic registration: Registration with registration target in a common coordinate system |
|
Individual sensor readings are brought into a common coordinate system during the set-up process |
|
Manual registration: Registration via golden sample |
|
|
With multi-sensor registration, the position of each individual scanCONTROL sensor is determined and transferred to a common overall coordinate system. Registration brings the individual sensor readings into a common coordinate system during the set-up process.
Micro-Epsilon offers an individual registration target for each measuring range of the scanCONTROL sensors and for each measuring arrangement. A special registration target can be designed for individual configurations and measurement setups. The sensors can also be registered without a registration target using a golden sample.
|
|
Applications
|
|
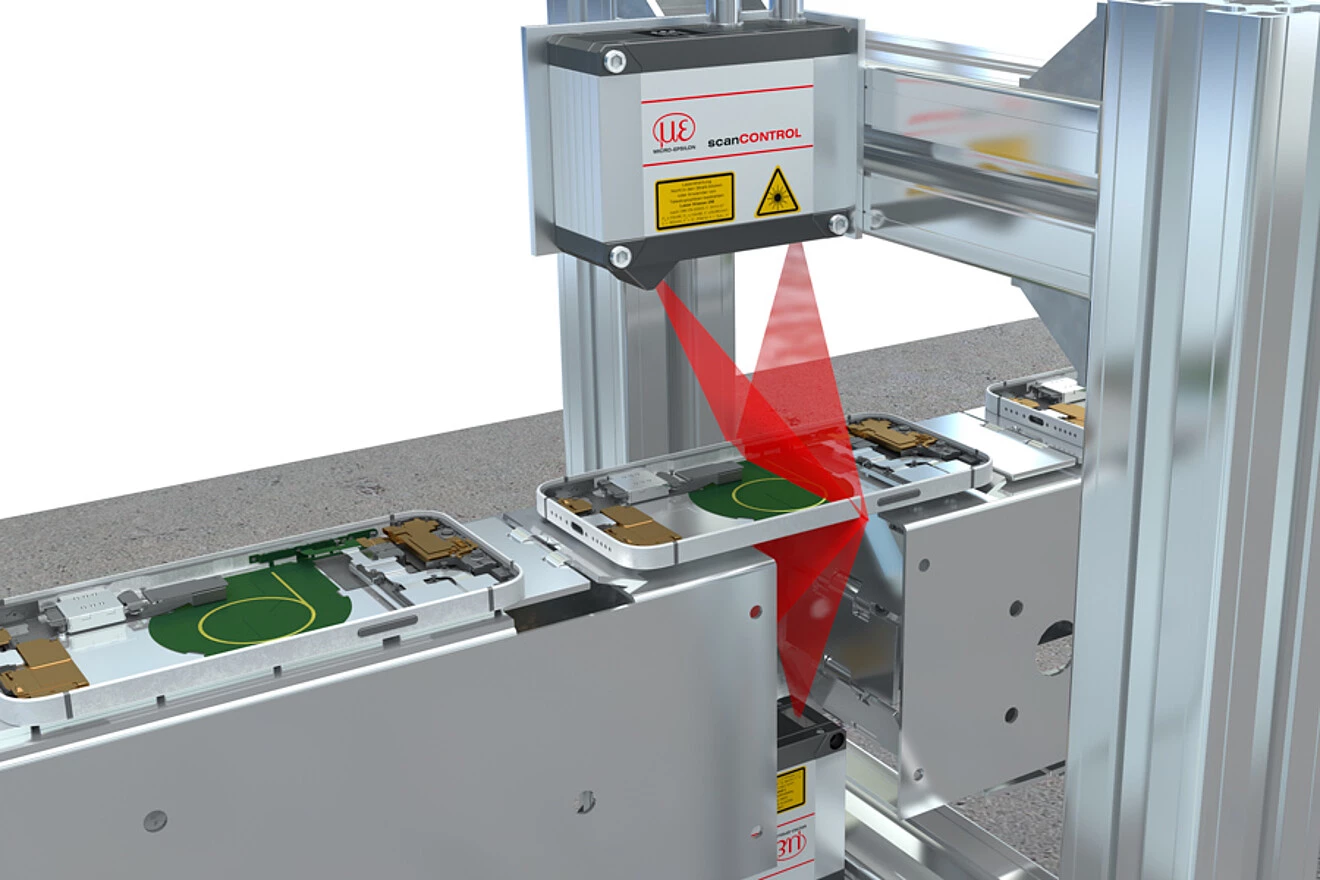 |
|
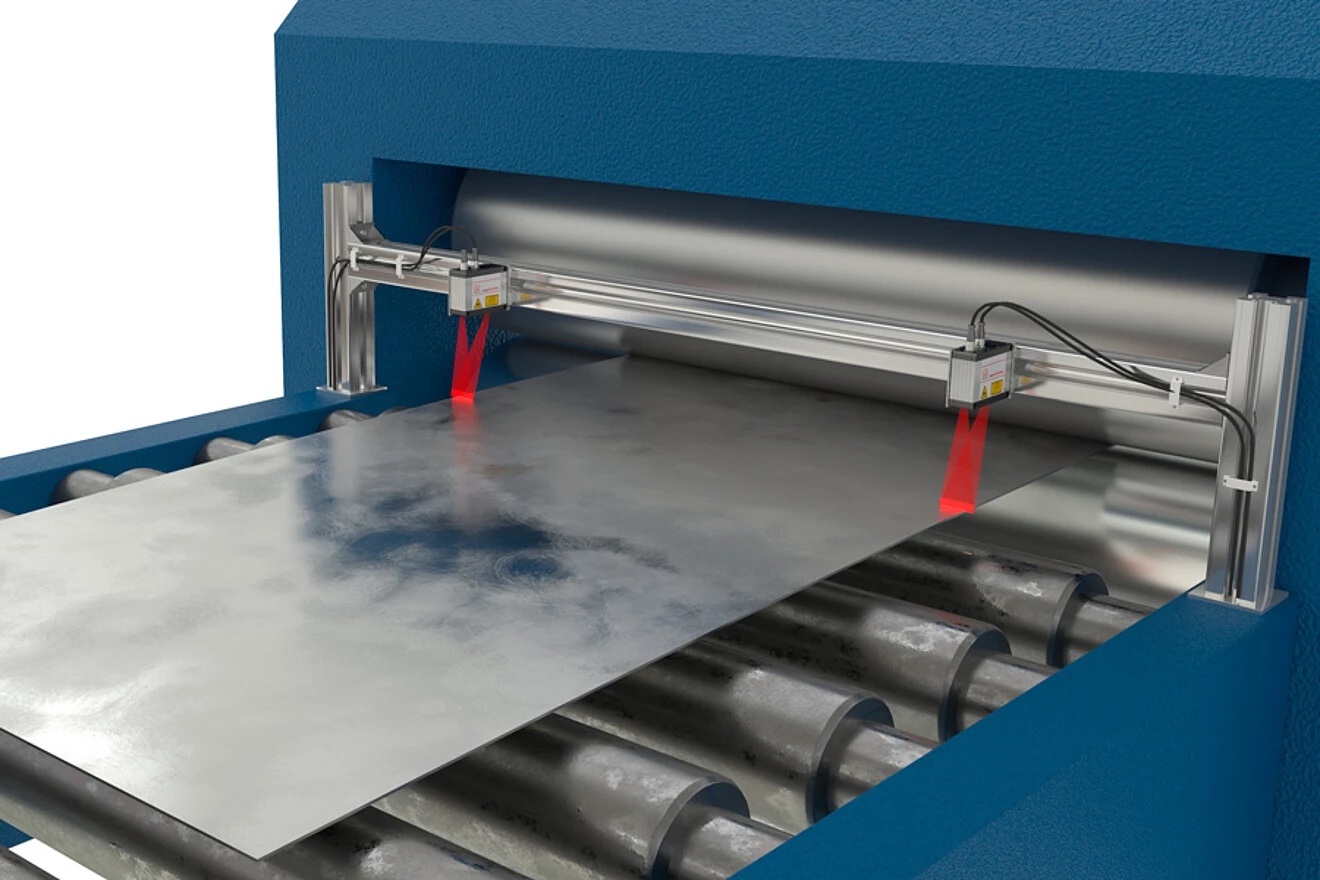 |
|
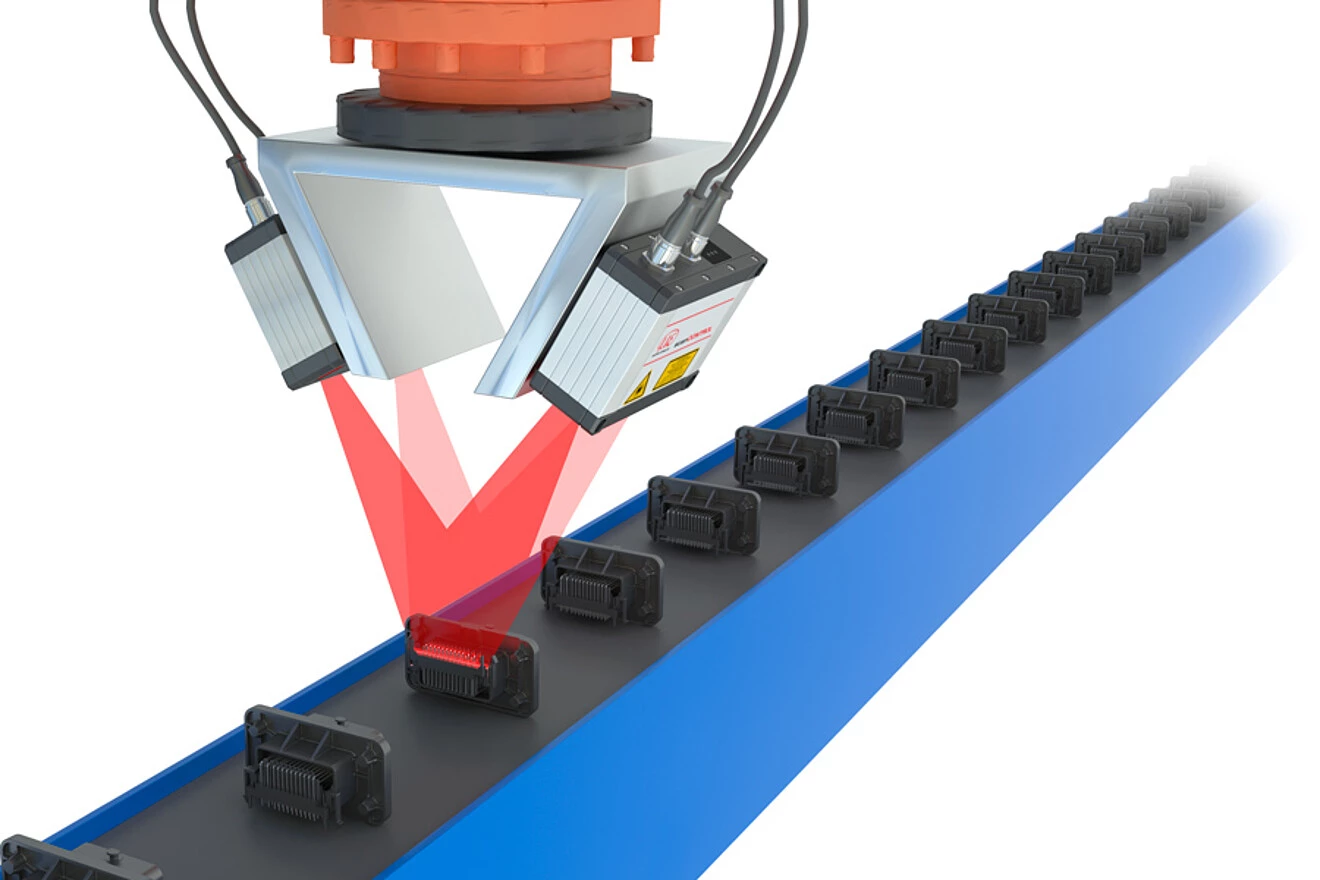 |
|
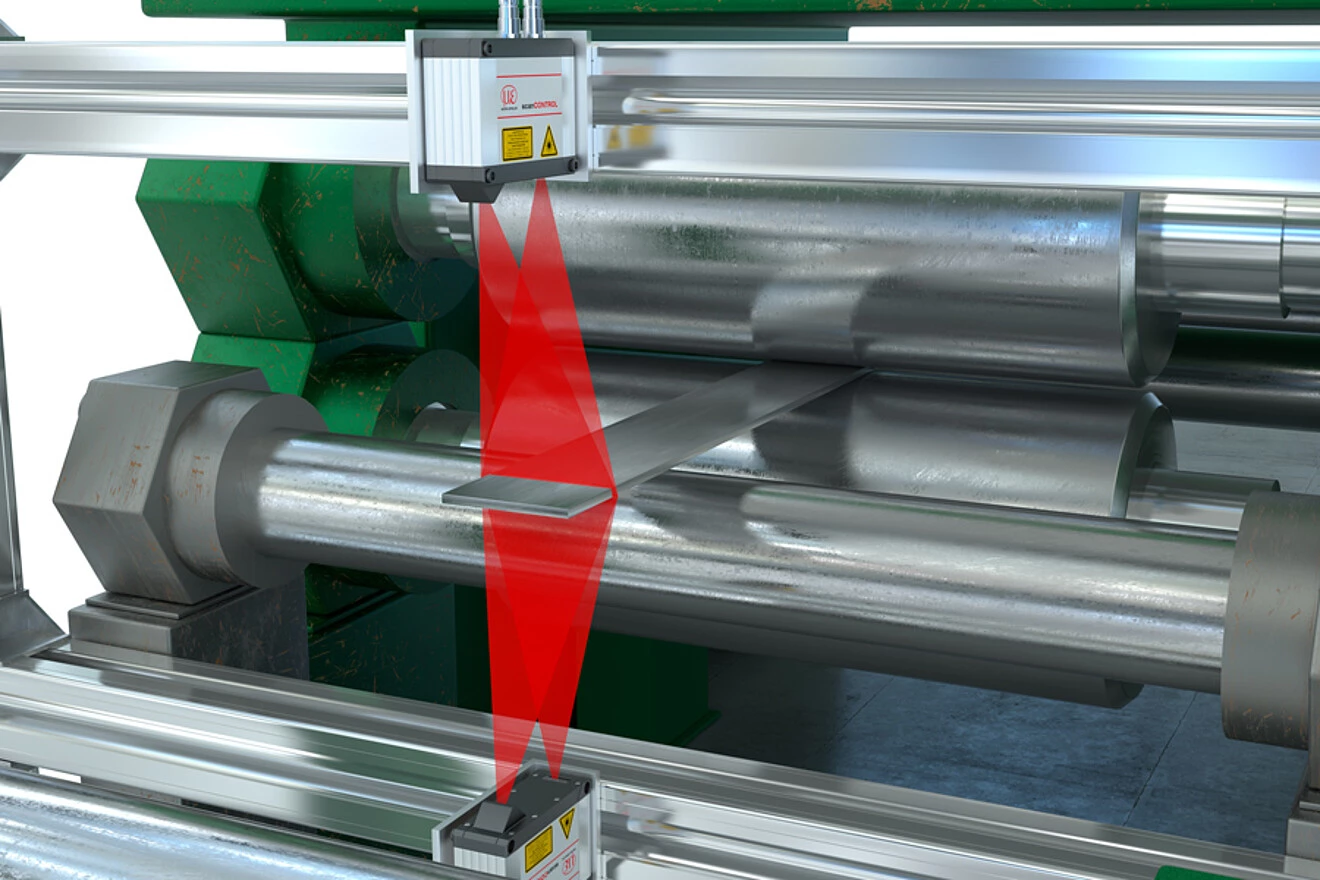 |
Thickness of smartphone carrier plates |
|
Width measurement on cold-rolled sheet metal |
|
Pin test on automotive connectors |
|
Thickness measurement of rolled steel strips |
|
|
|
|
|