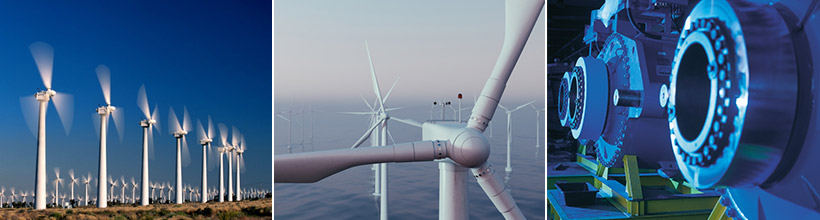 |
|
Energy technology: wind power, generators, large motors
|
In order to ensure high efficiency in power plants and large motors, predictive maintenance is an essential factor. Therefore, very high requirements are placed on the sensors in terms of accuracy, reliability and compactness. Sensors from Micro-Epsilon have proved invaluable with regards to safe plant operation in the test bench and in high volume applications. |
|
Mobile oscillation measuring system for wind turbines
|
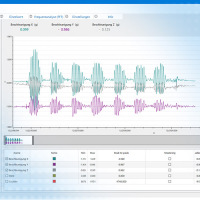 |
Test, inspection and certification authorities offer mobile oscillation measuring systems for wind turbines without permanently installed Condition Monitoring Systems. They are used for prototype plants in the development phase, for production and construction supervision, as well as for measurements during operation. In mobile vibration measurement systems, high-precision and temperature-stable acceleration sensors from Micro-Epsilon are used. The acceleration sensors provide precise information about vibrations that can occur, for example, at the rotor, tower or generator.
|
|
|
Noise reduction in wind turbines
|
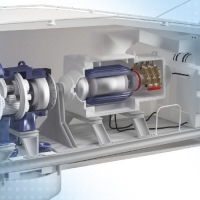 |
Wind turbines generate environmentally friendly power, but are often rather unpopular with their residents in the neighborhood, as they also generate noise. One of the noise sources in wind turbines is the drive train. In particular, gears and generators create noise. In order to minimize this noise, different measures can be taken. To measure these oscillations and evaluate the effectiveness of noise reduction measures, acceleration sensors from Micro-Epsilon are used.
|
|
|
Oscillation measurement of the drive train in wind turbines
|
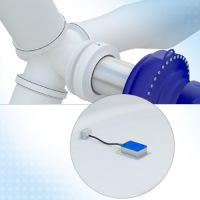 |
Oscillation of the drive train (rotor imbalance, overloading) exceeding the limit values may lead to a failure of components and plant parts. Prerequisite for early recognition of damage and for predictive maintenance is the safe and accurate oscillation measurement of the rotor bearing, gearbox (rolling bearings, gear wheels) and generator. To measure these oscillations, high-precision and temperature-stable acceleration sensors from Micro-Epsilon are used.
|
|
|
Measuring the bearing gap in wind turbines
|
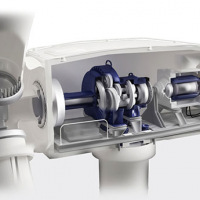 |
To date, bearing gaps were measured during standstill based on a tactile principle. Therefore, long inspection intervals were required, which in turn, may increase the risk of a complete plant failure. Moreover, these deliberate stoppages intended for measuring and inspection purposes cause considerable additional costs. Micro-Epsilon acquires the measurement values during plant operation, thereby enabling reliable, cost-saving real-time analysis. This measurement task is performed with the inductive eddyNCDT 3005 measuring system based on eddy currents. It includes a sensor with a measuring range up to 6 mm, which is permanently connected to the controller via a 1 m long cable. As the system is oil-tight both on the front and rear side, it is ideally suited to this application even when typical oil pressures reach 1 to 2 bar in the bearing. The eddyNCDT 3005 inductive system is already being used in wind turbines to analyze and optimize the maintenance intervals of wind turbines. In addition, the data acquired in the test bench throughout the design period can be taken into account and used for dimensioning purposes of new components. The sensors can be used in the test bench and in high volume applications for Condition Monitoring. Serial use offers major advantages as the sensor technology can already be aligned and precisely adjusted during installation and initial operation.
|
|
|
Rotor stress tests in the test bench
|
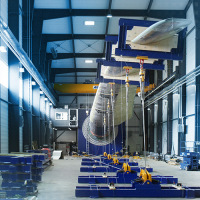 |
Test rigs have been developed for load tests on wind turbine rotor blades and simulate the real loads caused by high winds and weather. The tip of the rotor blade can be distorted by up to 10m due to mechanical loads. Draw-wire sensors are used on the test rig for measuring the distortion. Two sensors per traction point measure the deflection and torsion of the rotor blade. The draw-wire sensors operate with measuring ranges between 3 m and 10 m. The digital signal output is provided for further simulations.
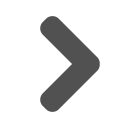 Draw-wire displacement sensors
|
|
|
Rotor gap measurement in the generator
|
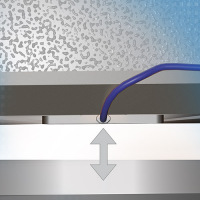 |
In order to monitor rotor behavior in the generator, capacitive displacement sensors measure the gap between stator and rotor. Despite high temperatures and electromagnetic fields, capacitive sensors from Micro-Epsilon provide unmatched accuracies. In addition to continuous measurement for predictive maintenance, the measurement can also be used when setting the generator.
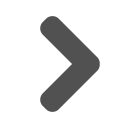 Capacitive displacement sensors and measurement systems
|
|
|
Monitoring the air flap openings
|
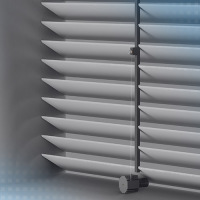 |
In order to control air supply, the air flaps automatically open and close depending on the temperature. Draw-wire displacement sensors monitor the position of the open air flap.
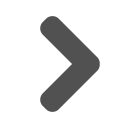 Draw-wire displacement sensors
|
|
|
Alignment of solar panels
|
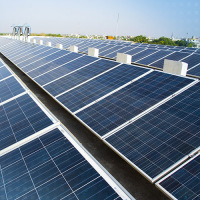 |
Aligning solar panels in relation to the course of the sun increases the energy yield, and therefore the plant effectiveness. Inclination sensors ensure that the panels are always properly aligned.
|
|
|
Monitoring the tower oscillation
|
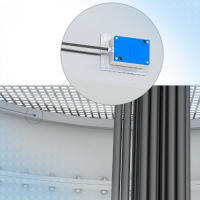 |
Wind turbines are exposed to oscillations and shock loads. In order to avoid damage and expensive downtime, these tower oscillations are monitored. When exceeding limit values, the plant is reliably shut down. From load history, lifetime prediction can be deduced. Prerequisite is the reliable and accurate detection of loads. Inclination and acceleration sensors from Micro-Epsilon detect the tower oscillation to the highest precision. Even with strongly fluctuating temperatures, inclination and acceleration sensors provide reliable measurements due to their excellent temperature stability.
|
|
|
Supporting moments of the nacelle
|
|
|
Measuring the foundation movement
|
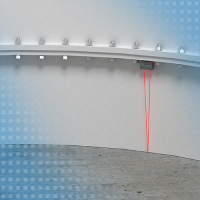 |
Laser triangulation sensors measure the distance from the foundation in order to detect the tower movements. High measuring rates enable to detect vibrations directly. Depending on the number of sensors installed, detailed evaluations about the vibration behavior can be determined. When the tower movement is too strong, the rotor blades are removed from the wind in order to avoid possible damage.
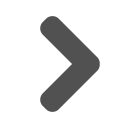 Smart laser triangulation displacement sensor
|
|
|
Measuring the deflection of the clutch disc
|
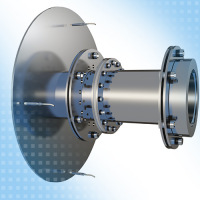 |
Eddy current displacement sensors measure the axial, radial or tangential deflection of the clutch disc. These robust sensors are designed for harsh ambient conditions and, due to their extremely compact size, can also be integrated in restricted installation spaces. The sensor provides stable measurement results despite high pressures and temperatures.
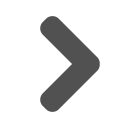 Inductive sensors (eddy current) for displacement, distance & position
|
|
|
Measuring the temperature of frictional heat on bearings
|
|
|
Oil gap measurement in shafts
|
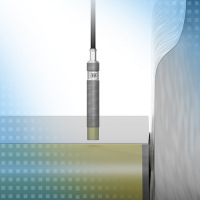 |
With regard to predictive maintenance, the oil gap should be measured, i.e. the distance between the bearing surface and the shaft filled with lubricants. Despite pressure, high temperatures and lubricants, robust eddy current sensors from Micro-Epsilon can provide a permanent statement about the lubricating gap based on high measurement accuracy.
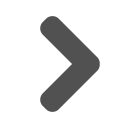 eddyNCDT 3001
|
|
|
|