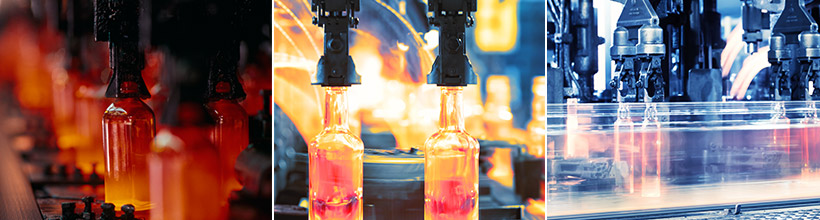 |
|
Glass production
|
Products such as container glass, flat glass or special glasses require tight manufacturing tolerances while maintaining the shortest possible production cycles. Due to the high degree of integration as well as the high accuracy and measurement speed, sensors from Micro-Epsilon are often used in the glass industry: robust inductive sensors are integrated into machines in order to detect machine movements while optical sensors monitor the glass products in processing lines. Typical measured parameters include displacement, position, thickness, color and temperature. |
|
Presence monitoring and identification of bottles
|
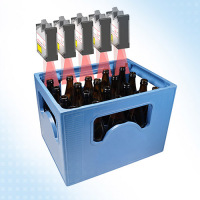 |
Laser scanners from Micro-Epsilon are used for high speed and fully automatic inspection of empty containers at bottlers and breweries. For this application, the Micro-Epsilon agent Tipteh has designed a test system based on laser line triangulation, which is used when the bottle crates are received. This inline system is equipped with five scanCONTROL 2900-50 laser line triangulation sensors from Micro-Epsilon. The crates are conveyed on a belt and scanned from above. Each scanner measures a row of bottles in the crates. Presence monitoring is carried out at conveyor speeds of up to 850 mm/s. The scanner uses the respective bottle height to determine whether the correct type of bottle is in the crate. The bottle height must not deviate more than 3 mm from the target height of the respective bottle type. Compared with a solution based on conventional image processing systems, laser scanners from Micro-Epsilon not only monitor bottle presence but also bottle height. In addition, logged data for subsequent statistics, evaluations and process optimization can be acquired.
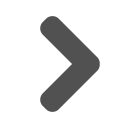 Laser scanners for 2D/3D profile measurements
|
|
|
Marking detection on cosmetics bottles
|
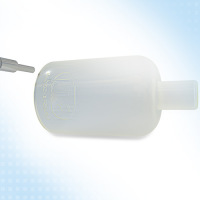 |
Before the printing process, a reference mark is embossed into the bottles. Due to the depression of the embossment, the color of the reference mark deviates slightly from the rest of the bottle surface. The colorSENSOR CFO100 detects this minimal color difference, which enables the exact determination of the printing position below the embossment. For a flawless print, accurate and reproducible positioning is crucial. If the marking is missing, the bottle is considered as faulty and will be rejected immediately. Therefore at the same time, a good / bad evaluation can be carried out as part of a quality control. A machine turns the cosmetics bottle while the colorSENSOR CFO100 constantly measures the surface of the bottle at a distance of less than 10 mm. The embossment is detected quickly and reliably. Next, the exact position for the bottle printing is determined and further process steps can be carried out. The colorSENSOR shows clear advantages over other measuring methods. First, it masters the semi-transparent surface easily. Second, it is ideally suited to this kind of position measurement task due to its favorable price/performance ratio.
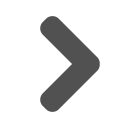 Compact True Color Sensor
|
|
|
Measuring the curvature of lenses
|
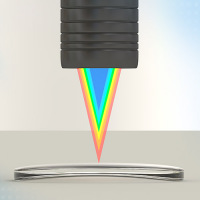 |
In order to meet production tolerances, the contour of optical lenses such as eyeglass lenses or objectives, confocal chromatic sensors are used. Based on the distance values, statements about the surface properties can also be made. The sensors enable a large tilt angle which means they can also detect highly curved surfaces.
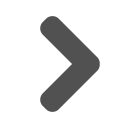 Confocal sensor systems for displacement, distance, position and thickness
|
|
|
Measuring the center thickness of lenses
|
|
|
Wall thickness measurement of container glass
|
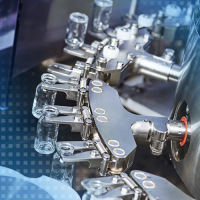 |
With the wall thickness and roundness measurements in star wheel inspection machines, a fast measuring rate is required in order to support the ongoing process. Micro-Epsilon’s confocal chromatic measuring systems provide a high measuring rate and fast exposure time control. This also enables the measurement of thickness when the glass colors vary.
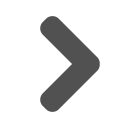 Confocal sensor systems for displacement, distance, position and thickness
|
|
|
Temperature monitoring from the melting material to the cooling process
|
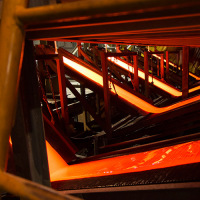 |
After the tin bath, flat glass has a temperature of approx. 600 °C. At the transition to the cooling zone and in the other subsequent cooling zones, thermoIMAGER infrared cameras are used for temperature inspection. Infrared cameras enable non-contact temperature monitoring of the cooling process from a safe distance to the glass. Thanks to the TIM Connect Software, the thermoIMAGER cameras can also be used as line scan cameras. The software enables the user to choose any line from the detector array and to position it.
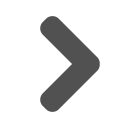 Thermal imaging cameras for industrial temperature monitoring
|
|
|
Gap monitoring of safety glass
|
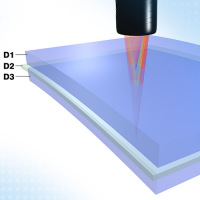 |
For quality control and process control during the production of safety glass, confocal chromatic displacement sensors with a multi-peak function are used. Confocal chromatic sensors from Micro-Epsilon enable thickness measurements to micron accuracy. confocalDT sensors detect up to 5 layers by evaluating 6 measurement values on the boundary areas.
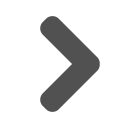 Confocal sensor systems for displacement, distance, position and thickness
|
|
|
Roundness of bottles
|
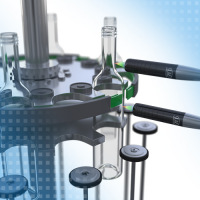 |
With the roundness measurement of container glass, a fast measuring rate is required in order to support the ongoing process. Confocal chromatic sensors from Micro-Epsilon are used for thickness measurements in the star wheel while providing high measuring rates and accuracy in order to ensure reliable operation.
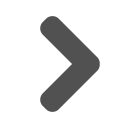 Confocal sensor systems for displacement, distance, position and thickness
|
|
|
Plunger stroke in IS machines
|
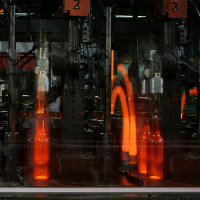 |
For 24-hour operation in the glass production involving more than 5 million measuring cycles pear year, Micro-Epsilon has developed an inductive EDS displacement sensor. This sensor determines the exact plunger position in IS machines and allows for the production to be carried out according to predefined specifications. In order to increase resistance to lubricants and shock loads, the entire sensor and electronics are now welded into a tight stainless steel housing.
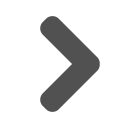 induSENSOR EDS
|
|
|
|
Color measurements of glass shades
|
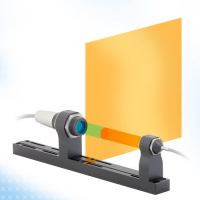 |
The color is the crucial and visually distinctive feature of glass products. This is particularly true with natural and recycled raw materials based on varying compositions, where continuous and objective control of the color effect is an essential prerequisite for consistent quality. The ACS3 transmission sensor from Micro-Epsilon is used to inspect the glass colors and shades continuously.
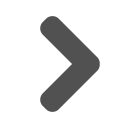 High Speed Photospectrometer colorCONTROL ACS7000
|
|
|
|
Planarity and thickness of display and flat glass
|
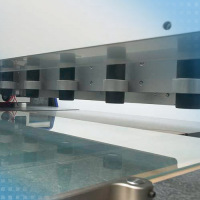 |
For the production of display glass, glass sheets with consistent thickness are required. The production process is regulated based on the measured results. Confocal chromatic sensors from Micro-Epsilon are used to detect the thickness from one side. Due to their high measuring rate, the sensors are also applied in high speed processes. When the sensors operate in a traversing manner or in several tracks, the planarity of complete sheets can be documented.
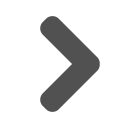 Confocal sensor systems for displacement, distance, position and thickness
|
|
|
|
Thickness of glass coatings
|
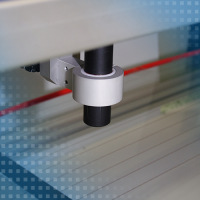 |
Glasses are often reinforced with safety and security films which provide increased splinter protection. In order to measure the film layer and to determine the thickness of the applied adhesive, confocal chromatic sensors from Micro-Epsilon are used. These measure the thickness of the finest of layers from one side. With one measurement, the thickness of the glass, film and the applied adhesive can be determined.
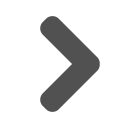 Confocal sensor systems for displacement, distance, position and thickness
|
|
|
|
Surface inspection of display glass
|
|
|
|
Edge measurement of glass
|
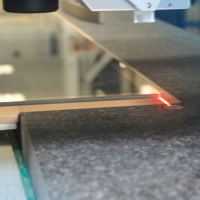 |
In many handling processes, precise positioning of glass sheets is required. The position of the sheets is determined via the detection of the glass edges. Laser profile sensors from Micro-Epsilon measure the edge position at several points and transmit this information to the control system.
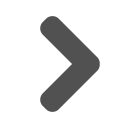 Laser scanners for 2D/3D profile measurements
|
|
|
|
Distance control of print heads for glass printing
|
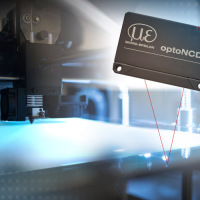 |
When printing on materials such as glass and ceramics, very fine detailed structures are applied on the carrier material, which requires precise positioning of the print head. For distance measurements, optoNCDT 1420 laser triangulation sensors from Micro-Epsilon are used. With a measuring range of 10mm, these determine at various points in the print head the respective distance from the surface to be printed. The data obtained enables the determination of the edges and the surface tilt and therefore the exact positioning of the print head.
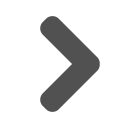 Smart laser triangulation displacement sensor
|
|
|
|
Non-contact temperature measurement when shaping container glass
|
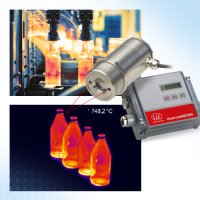 |
In container glass production, the process relevant temperature must be inspected at different points. Non-contact temperature sensors are used during the shaping process that involves temperatures in excess of 500 °C. As the shaping process lasts for just a few seconds, the sensor response time is critical. During both the forming process of the parison and the final shaping process, the heat treatment of the glass can be influenced either by directly measuring the glass surface or by indirectly measuring the surface of the forming tool. At the end of the production process, the glass is tempered again to reduce the stress in the container. Therefore, the glass is heated again and then cooled for a period of up to 30 minutes in a cooling tunnel. When the containers leave the heating zone, the cooling process is monitored using non-contact temperature sensors.
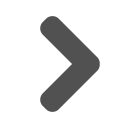 Infrared pyrometer with laser sighting for the glass industry
|
|
|
|
Bottom thickness measurement of container glass
|
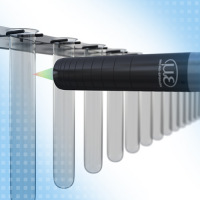 |
With the wall thickness and roundness measurements in star wheel inspection machines, a fast measuring rate is required in order to support the ongoing process. Micro-Epsilon’s confocal chromatic measuring systems provide a high measuring rate and fast exposure time control. This also enables the measurement of thickness when the glass colors vary.
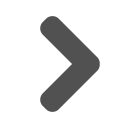 Confocal sensor systems for displacement, distance, position and thickness
|
|
|
|
Distance measurement onto anti-reflective coated glass
|
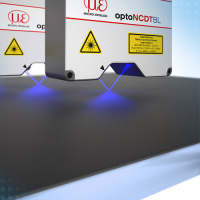 |
Anti-reflective coated glass is inspected during the coating process using laser-optical displacement sensors from Micro-Epsilon in order to determine undulations and torsion. The planarity of the coated glass surface is measured in several tracks. Based on the patented Blue Laser Technology, optoNCDT 2300-2DR sensors provide high measurement accuracies on coated glass surfaces.
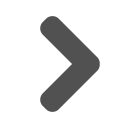 Blue Laser triangulation sensors for difficult surface types
|
|
|
|