Functional Safety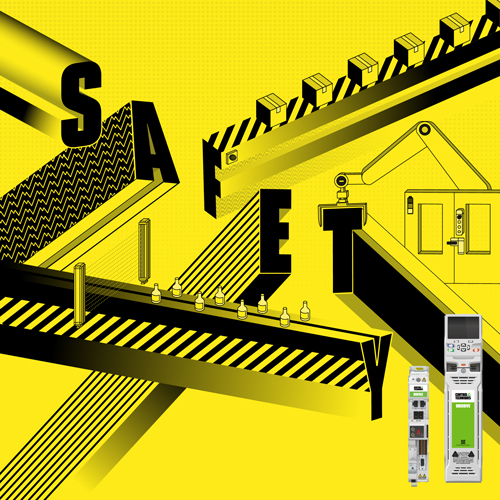
All Unidrive M drives have integrated dual Safe Torque Off (STO) inputs, certified to SIL3 / PLe, providing an elegant and reliable safety solution.
The addition of an MiS210 safety option extends the built-in STO with the ability to safely monitor and/or restrict the scope of motion.
Safety functions include: STO, SBC, SOS, SS1, SS2, SLS, SSM, SLA, SDI, SLP & SES
For maximum flexibility in the safety system architecture, the modules support both wired and network safety connections: CIP-Safety on EtherNet/IP and Safety over EtherCAT (FSoE).
To find out more, visit our Functional Safety page.